Pictures and links to pictures below and I would like to thank Andy Mitchell of Mitchell Motors in Wiltshire for allowing me to post the pictures on the forum. He will be competing later this year.
Start to finish of the project was 2/3 months.
The pictures show what the bodywork will look like and the former created to make the bodywork in virtual and real life.
Estimated time saving for Andy will be 35%. Accuracy massively improved. If car is crashed, he has the ability to recreate the bodywork exactly as it was before.
"Virtual" finished buck.
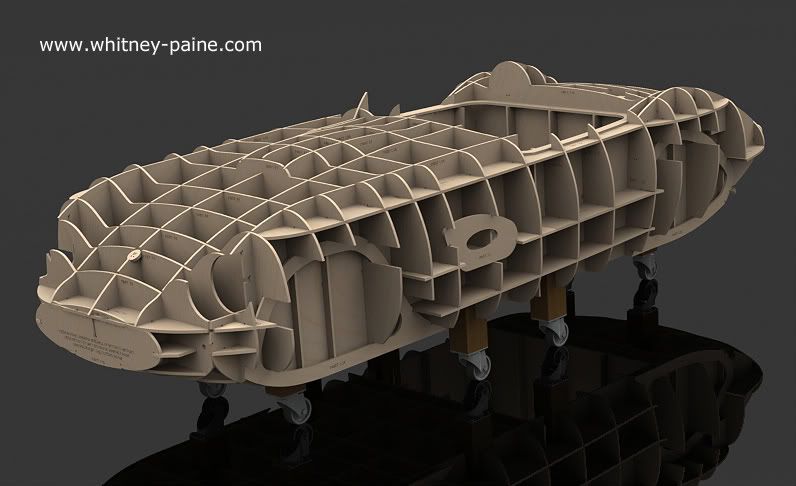
Finished buck in real life.
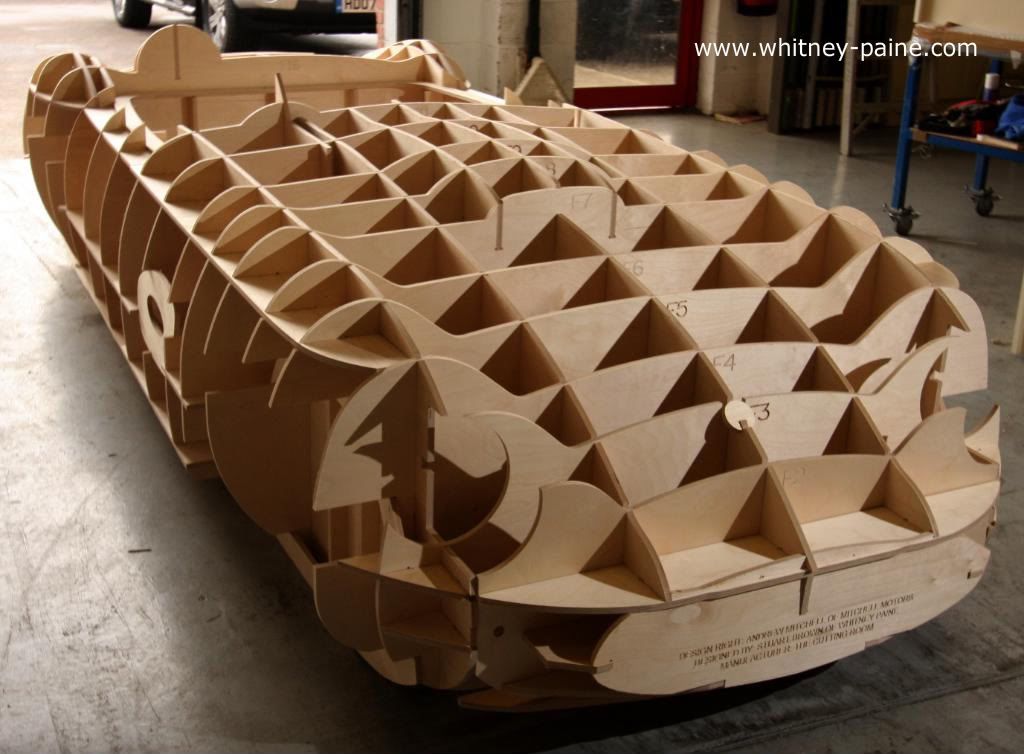
"Virtual" bodywork as it will look when car created in the flesh...colour to be decided.
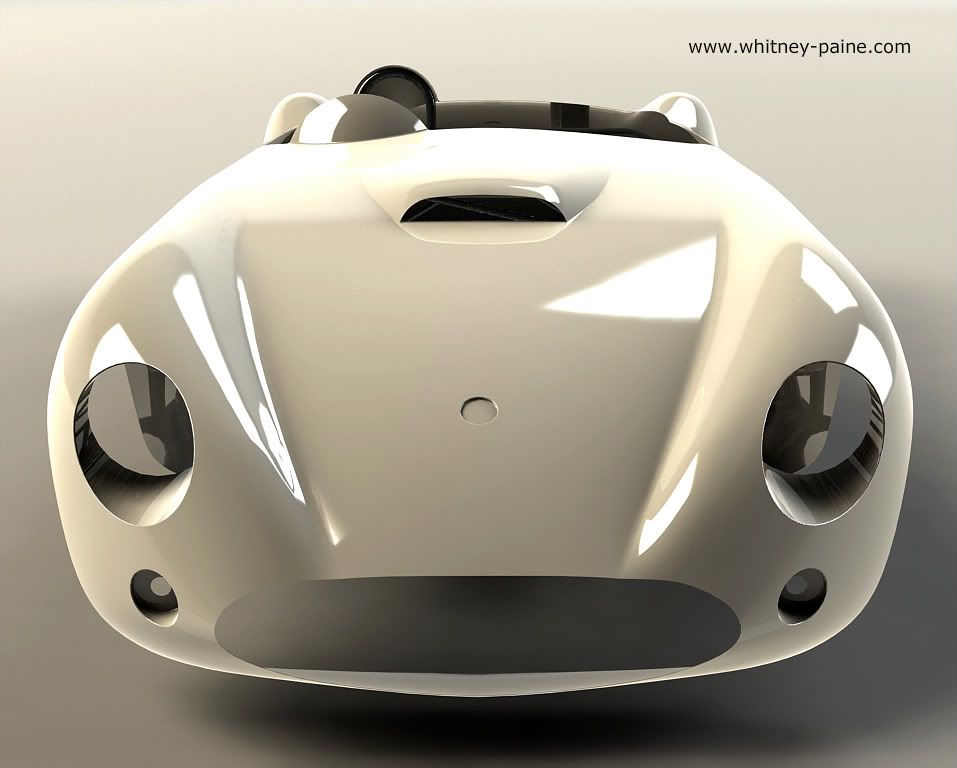
Real buck/former - close up rear view.
http://i264.photobuc...-manipulate.jpg
"Virtual" tubular chassis.
http://i264.photobuc...ame-VS1copy.jpg
"Virtual" bodywork with tubular chassis added.
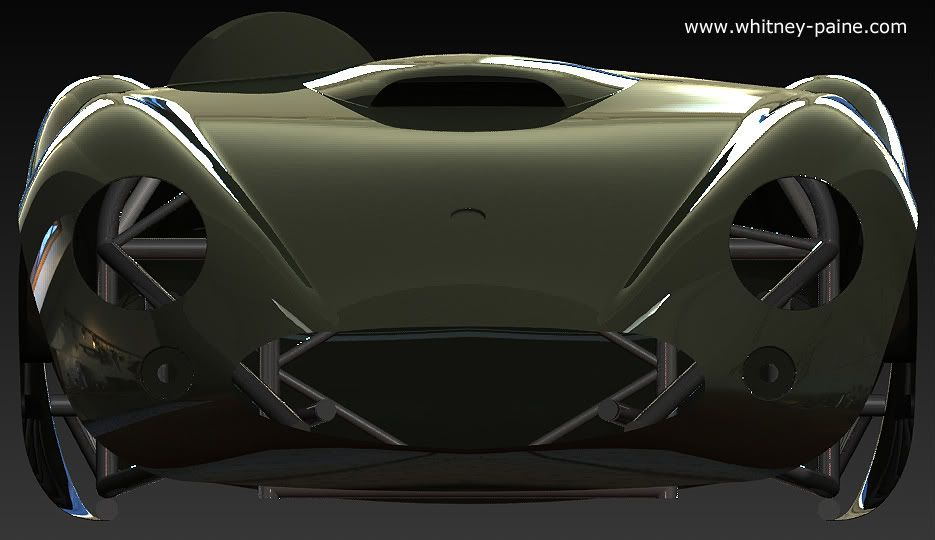
"Virtual" rear view of bodywork.
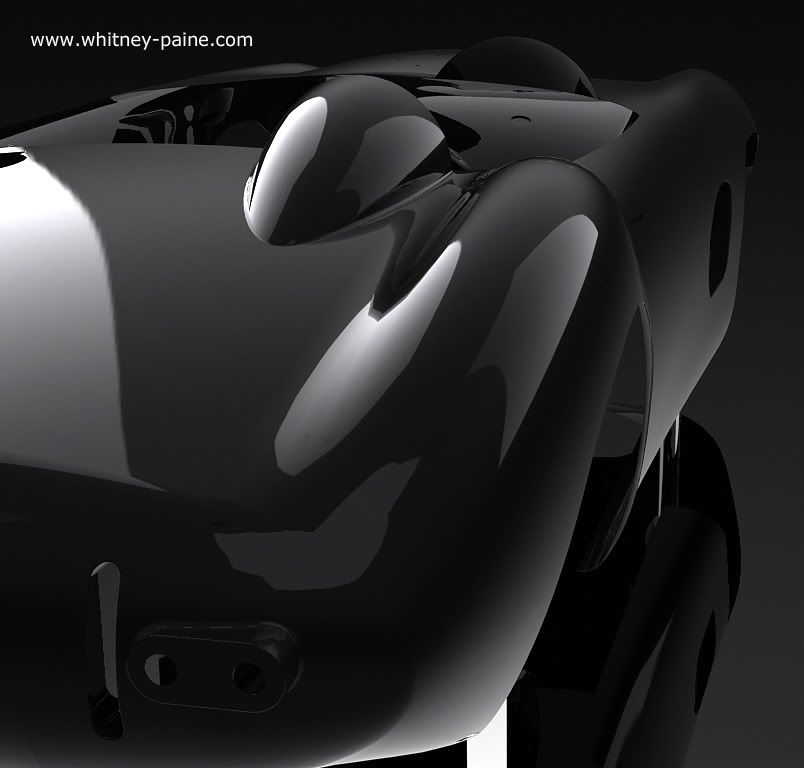
Real buck - corner close up.
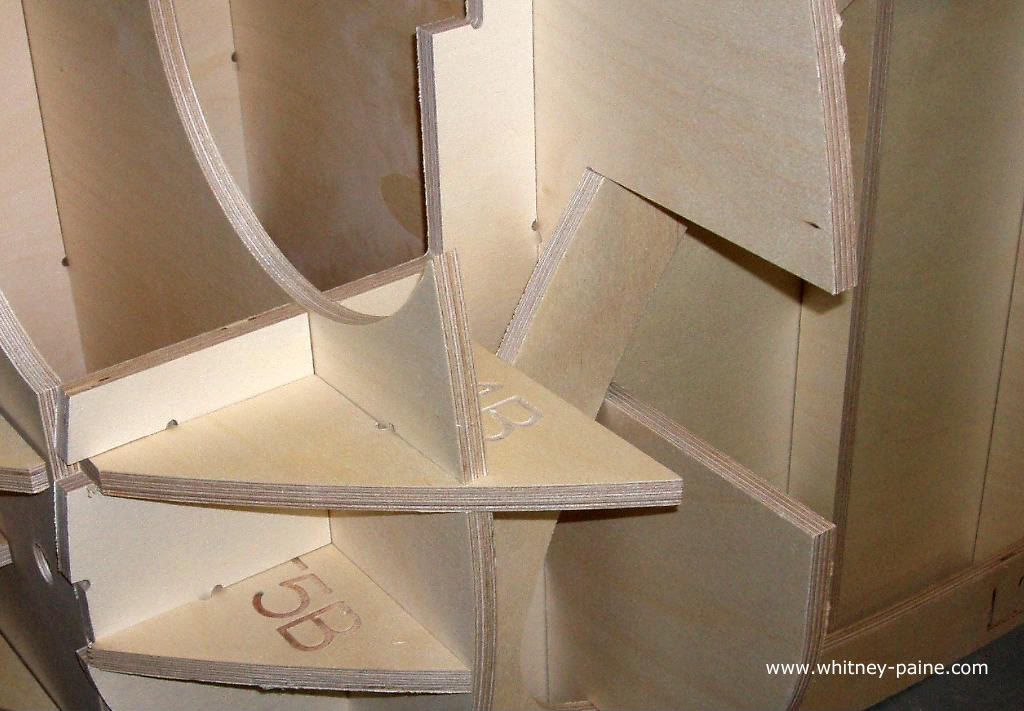
Virtual corner close up....very close I reckon...as you would expect.
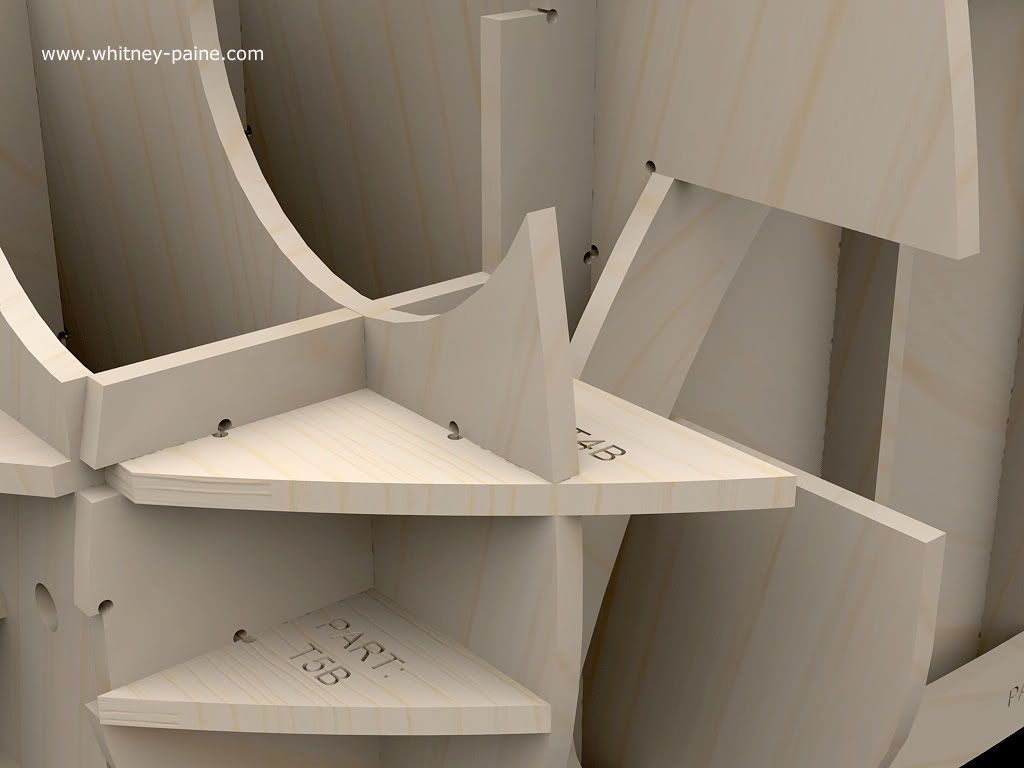
Real hoop former.
http://i264.photobuc.....g car/b11.jpg
Real view over front of buck.
http://i264.photobuc.....g car/b13.jpg