
Diffuser Volume and Angle
#1
Posted 27 June 2012 - 03:54
I know the diffuser slows down the speed of the airflow. By why is a bigger diffuser in terms of geometric volume better (such as the double diffuser)? This question has bothered me for some time.
Does a bigger diffuser speed up the airflow under the car ? Why ?
What fluid dynamics principles apply here ? What is the purpose of the tea tray splitter at the front ? Why is there no diffuser at the front of the car ?
Many thanks to all of you.
Advertisement
#2
Posted 27 June 2012 - 04:01
#3
Posted 27 June 2012 - 06:32
Why is there no diffuser at the front of the car ?
It has been made front diffusers for the Prototype cars. Lola i think pioneered it.
They also do it today. but in a different way, as the old design used the same air that went out at the back.
http://lemansprototy...1-69413568.html
http://lemansprototy...02-6139447.html
Thats why they lift a section of the front splitter.
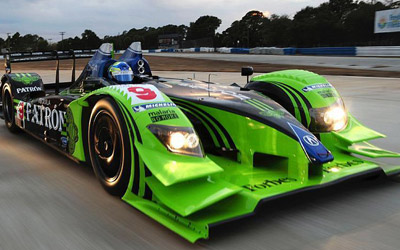
F1 would have done this if they where allowed to have a wider nose/front.
The tea tray does at least stop air from being forced underneath the car.
Edited by MatsNorway, 27 June 2012 - 06:34.
#4
Posted 27 June 2012 - 14:31
#5
Posted 29 June 2012 - 00:39
I don't know what you mean by a double diffuser.
bear in mind you'll get separation at some critical angle of the exhaust, probably around 7 degrees, for the sake of argument.
#6
Posted 29 June 2012 - 07:22
bear in mind you'll get separation at some critical angle of the exhaust, probably around 7 degrees, for the sake of argument.
6/7 degrees for 2D on a 3D with strakes you can go up to 16.7degrees.
#7
Posted 29 June 2012 - 11:18
#8
Posted 30 June 2012 - 08:28
no matter how much bigger the diffuser is made ? Like a pipe I mean ? Say 3 sectioned pipe with section 1 radius = 5 cm , section 2 radius = 2.5 cm and section 3 radius = 5 cm >> IF
increase section 3 radius to 7.5 cm will the constant mass flow rate for the whole pipe increase or will section 2 STILL act as bottle neck to limit flow ? Many thanks.
#9
Posted 30 June 2012 - 22:38
No it doesn't act as a bottle neck as such at typical racing speeds, but it will increase the duct drag, which you won't have in your model.
#10
Posted 30 June 2012 - 23:30
How does constant mass flow rate work ? I mean specifically does the flow for the whole underfloor increase with a bigger diffuser or does the floor/venturi act a bottle neck that limits flow rate
no matter how much bigger the diffuser is made ? Like a pipe I mean ? Say 3 sectioned pipe with section 1 radius = 5 cm , section 2 radius = 2.5 cm and section 3 radius = 5 cm >> IF
increase section 3 radius to 7.5 cm will the constant mass flow rate for the whole pipe increase or will section 2 STILL act as bottle neck to limit flow ? Many thanks.
pbukovca-
The typical underbody diffuser on a race car functions like an extractor duct. It creates a region of low dynamic air pressure under the body.
Here's how they designed diffusers before PCs and CFD software:
http://hdl.handle.net/2060/19930083792
Regards,
Slider
#11
Posted 01 July 2012 - 04:22
pbukovca-
The typical underbody diffuser on a race car functions like an extractor duct. It creates a region of low dynamic air pressure under the body.
Here's how they designed diffusers before PCs and CFD software:
http://hdl.handle.net/2060/19930083792
Regards,
Slider
Remarkable what was done with sliderule/analog tech.
#12
Posted 01 July 2012 - 04:39
Digging through old NACA reports is very interesting (and that one looks like a classic). Here's the NACA / NASA report server. http://ntrs.nasa.gov/?method=aboutntrs , not much is directly applicable to cars, but it is a great engineering resource.
#13
Posted 01 July 2012 - 05:07
Remarkable what was done with sliderule/analog tech.
desmo,
That tech paper was written by a couple of Stanford University post grads. The founders of the Hewlett-Packard corporation were also both Stanford grads. I have an HP-15 engineering calculator that I still use every day, and it is over 25 years old. See the pattern here?
#14
Posted 01 July 2012 - 05:34

#15
Posted 01 July 2012 - 20:12
Here's how they designed diffusers before PCs and CFD software:
http://hdl.handle.net/2060/19930083792
that was 1953 report
when was the first underbody aerodynamics in race car design ?
#16
Posted 01 July 2012 - 22:02
http://lemansprototypes.over-blog.it/
#17
Posted 04 July 2012 - 02:35
My mother and father are both Stanford grads, as are a grandmother, a grandfather and even a great-grandmother who was in the first coed graduating class.
desmo,
The aerospace engineering company I currently work for actively recruits Stanford post grads. Stanford has a long history of producing a very high quality technical product. The university has also not given in to the disturbing recent trend among US universities of corrupting their science with political correctness.
slider
#18
Posted 04 July 2012 - 02:49
Odd that.
#19
Posted 04 July 2012 - 04:34
desmo,
"recent trend among US universities of corrupting their science with political correctness."
What do you mean by this?
Advertisement
#20
Posted 04 July 2012 - 05:37
Is there any benefit in smoothing the transition between the throat and the exhaust?
Edited by Greg Locock, 04 July 2012 - 05:55.
#21
Posted 04 July 2012 - 10:22
Greg, yes smooth transition is better.
Read this: How wings work
It's a famous paper by Babinski. It explains the curved streamline theory.
Some at the top asked about if the 16.7 included the wing low pressure: No it does not. (check for a work by Andrea Ruhrmann, Uni of Southampton, PhD Thesis, for information on diffusers.
Greg concerning how come the critical angle is different I believe it has something to do with the vortices produced by the side of the diffuser tunnel and the strakes. The vortices induce upwash, which prevents the flow from separating from the diffuser surface. (my area is front wings not diffusers, but suspect that is what happens...).
Edited by Monstrobolaxa, 04 July 2012 - 10:22.
#22
Posted 08 July 2012 - 00:55
Interesting paper.
These are few papers of a former lead aerodynamicist at Boeing, Arvel Gentry, who has been preaching the same in sailing in more layman terms:
The aerodynamics of sail boats are becoming quite complex. I know an aero guy that is working for a kiwi Americas' Cup team. He calls them wings instead of sails. It's amazing that these "sails" can push the boats downwind at speeds greater than the prevailing wind.
#23
Posted 08 July 2012 - 04:37
#24
Posted 08 July 2012 - 22:53
But, if the wing pulls too much extra air through under the car then the acceleration will increase and the critical angle will reduce.
Howver since the whole thing is a system you can't really break it down like that.
Edited by Greg Locock, 08 July 2012 - 22:59.
#25
Posted 09 July 2012 - 07:15
I think, the guy you referring to, is Andreas Ruhrmann - short essay from his work can be found here
There were two people at Soton about that time.
Andrea Senior (female...who by marriage became Andrea Ruhrmann) who did a PhD on diffusers (I have a copy of her thesis in front of me) - I meant this one.
Andreas Ruhrmann (male) who also did research on diffusers!
Greg concerning you question: "are we talking about wings or diffusers?"
The paper I mentioned explains the transition from the flat bottom to the diffuser. And how being smooth and curved reduces the pressure in the transition. If it was sharp it would probably separate.
Edited by Monstrobolaxa, 09 July 2012 - 07:23.
#26
Posted 09 July 2012 - 13:16
#27
Posted 10 July 2012 - 01:40
I thought we were talking about diffusers, not wings.
Fair enough. Race car diffusers it is then.
One question posed in the OP was the relationship between underbody diffuser volume and divergence angle. With F1 cars many of the basic diffuser dimensions are tightly regulated, so there's not a whole lot that can be done with the volume of the diffuser duct. However, if there were no such regulations there would be significant benefit to making the diffuser volume large. A good example is the IMSA GTP cars of the late '80s and early '90s. These cars used massive underbody tunnels. In fact, the tunnels were so tall that the lower wishbones and driveshafts passed through them. These cars made huge downforce from the underbody.
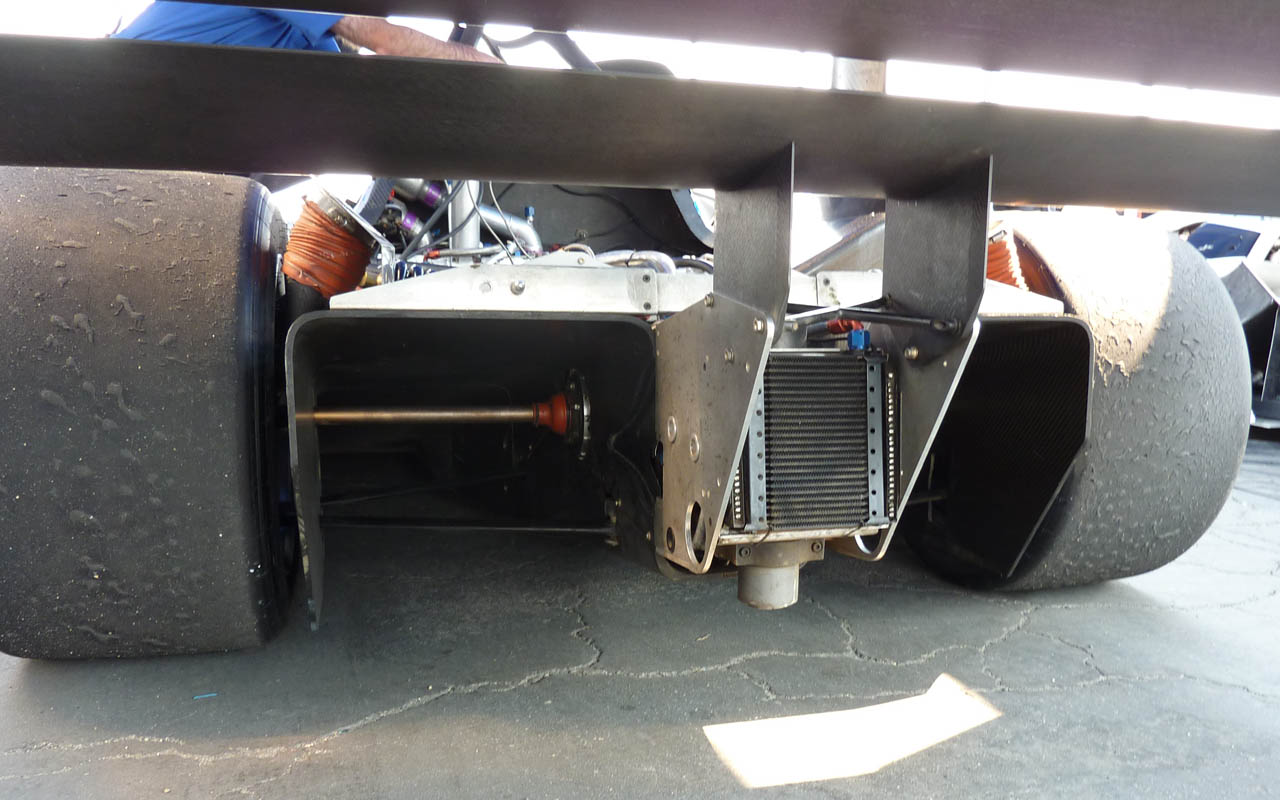
slider
#28
Posted 10 July 2012 - 22:38
#29
Posted 12 July 2012 - 00:02
I think the answer is that the fine detail of the underbody shape wouldn't make much odds. The reason I say that is that venturis are used all over the place, and yet their basic form, intake trumpet, parallel low pressure section, constant taper diffuser, scarcely varies. There is some variance in the trumpet design, but that Blair paper showed that at least on intake manifolds the gains from different shapes there were subtle at best.
That's true in some respects. Some types of diffuser designs are less problematic than others. One thing that makes diffuser design more/less difficult is what occurs ahead or behind the diffuser section. In this respect, an intake manifold or carb venturi is different from a radiator duct or an underbody.
Race car underbody diffuser design also presents a unique challenge in that one of the four walls of the diffuser duct is formed by the track surface. Three of the duct walls are moving relative to the airflow, and one is not. That certainly throws a monkey wrench into things.
slider
#30
Posted 12 July 2012 - 07:02
Edited by MatsNorway, 12 July 2012 - 07:06.
#31
Posted 14 July 2012 - 00:16
It might give new challenges in calculations considering the wall moves up and down. But it proably gives gains over a fully static one because the lower wall aids in moving the air. Rather than generate a umm. a boundary layer?
For being such a small portion of the total airflow those pesky boundary layers sure do have a big effect. Whether it's aerodynamic lift/drag or convective heat transfer, all of the real activity takes place in that tiny boundary layer flow. Whether this boundary layer flow is turbulent or laminar can have a big effect on L/D or heat transfer rate. It's a similar situation to that of the tiny tire contact patches. No matter how good the engine, suspension, brakes, aerodynamics, etc. of the car are, in the end it all boils down to how effective those four tiny tire contact patches are. The tire contact patches are the only interface to the track, and the boundary layer is the only contact with a heat exchanger fin, duct wall or wing surface.
#32
Posted 14 July 2012 - 01:55
#33
Posted 17 July 2012 - 17:53
Small video of a diffuser like shape in Autodesk Falcon.
Edited by MatsNorway, 26 July 2012 - 11:49.
#34
Posted 26 July 2012 - 11:49