
Rear wing positioning relative to Diffuser exit
#1
Posted 02 September 2008 - 21:10
The idea is to reposition the lower rear wing elements to best interact with the floor and diffuser exit. The car has a flat floor (no step plane) with the diffuser starting at the front of the rear wheels. Currently the lower rear wing element is (probably) too high and too rearward to interact effectively with the floor.
Can anyone offer any advice or rules of thumb as to a good reference position to start from? Measurements based on wing chord and / or diffuser exit height would be best. We would like to limit ourselves to maybe 5 options to test: forward, backwards, higher and lower, from the reference position.
We plan to conduct a straightline aero test measuring pushrod loads to determine the best configuration.
Regards, Ian
Advertisement
#2
Posted 03 September 2008 - 00:32
You might want to think about 'reserving' one test so you can do a final run based on the results of the other 4 .
If we put our engineering hats on we might find some value in a DOE, particularly if you start to worry about more factors, levels, or interactions. For instance in my work I often use first order interactions, and three levels for each factor. That'll need more than 4 runs, obviously.
(Late edit, well, no, recommendation for 4 runs, 2 factors at 3 levels is
Run Factor 1 Factor 2
1 M H
2 L M
3 H L
4 H H
for example, tho i haven't checked exactly what you'd get out of it. note that it is not balanced so analysis is not straightforward. Still that is fewer runs and more information)
Have you thought about a camera and wool tufts so you can at least figure out where the wing should be roughly?
#3
Posted 03 September 2008 - 03:57
First, you can make a lower element of a rear wing _really_ evacuate a diffuser exit. It can have a hell of a big effect, and it's almost free downforce. There's a bunch to be gained here.
Let's look at the pressure distribution field that is made by our airfoil. It'll look something like this (except upside down).
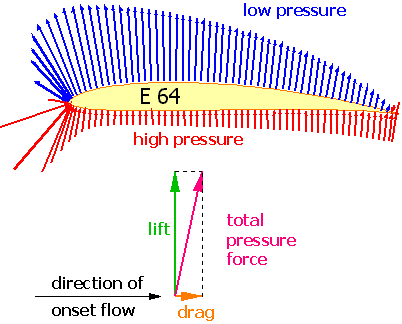
We want to position the wing close enough to the diffuser exit that it will add a bunch of energy to the flow at a point where it's going to be prone to separation. However, it has to far enough away from the diffuser to get good flow to it. Tidy bodywork at the back of the car will be a bonus here. Keep in mind, though, that evacuating the diffuser better will generally add front aero percentage. That is a little counter-intuitive. It's possible (although not likely in most cases) to add rear wing angle/gurney and actually increase front downforce percentage.
As you move the wing more forward, you lose the cantilever effect that you get over the rear wheels, so you limit the amount of front wing you can carry and maintain a reasonable balance (Hint: this is one reason why nearly all aero formula cars have ran more and more front weight, it lets you carry more front wing which means more overall downforce). As you move the wing up you get better flow to the wing and it acts better in it's own right. My guess is that you have a certain rear wing setback rule and a maximum height rule. I doubt if you'll come anywhere close to either. Since wings seem to be open in hill climbs, though, you might be able to get to the setback rule by running some heroic sized wings, I don't know.
I would bet that a dual element rear lower element would be a good starting point, and don't spare the gurney. Ya, it'll be draggy. It's a hill-climb. Unless you're carrying enough wing that your terminal velocity is 50 kph, you'll be faster with more wing. Try to choose an airfoil that has more localized and intense pressure depression rather than a more spread out, but even. That should let you move it a tick higher and more into cleaner air. Having said that, the foil also needs to be able to deal with dirty air since it's at the back of the car. It's got a tough job. That's another reason why a good sized gurney (20 or 25mm) is your friend. It'll keep that wing alive.
Put plenty of strakes in the diffuser, the closer you can keep it to 2-D flow, the better. Again, a difficult job. The angle of the floor itself is also a trick. Anyone can make a 5 degree floor work, but if you do the exit properly, you can get a hell of a lot more than that. If you've got a big wing back there on the exit, you can get pretty bold.
#4
Posted 03 September 2008 - 09:24
Murpia I have some high lift F1 foils somewhere on my computer, but these things get a bit sensitive and fiddly to manufacture...how are you going to make the wing?
BTW look here: http://www.ae.uiuc.e...database.html#E
#5
Posted 03 September 2008 - 12:43
I have a question based in logic but precious little knowlege of aero's.
In that (amazing NR and thanks) list there is a wing profile for a "human powered" wing. Now wouldn't that shape give the ultimate downforce for the slow speeds we are considering here?
..and by the way, how do you open those .dat files?
#6
Posted 03 September 2008 - 13:37
Thanks for the great repsonses, so here's some more detailed info (it's alwayd hard to know where to pitch the initial post).
The car already has twin element upper and lower rear wings. Each wing is the same mainplane and flap profile, with a gurney. The wings have been extensively tested and flow-vizzed to set angles that are 'good' but 'safe' (i.e. low risk of separation).
Drag is not an issue - we know that more downforce will improve performance down to an L/D of about 1.0...
A more forward aero balance is what we expect from a better working floor, that goes along with previous results from fitting barge boards. Again this is OK, we can re-balance if needed with the front wing.
We have to use the existing rear wings, so the test is all about best positioning of what we have. As I stated before we believe the existing lower rear wing could be lower and more forward in order to 'activate' the floor better. We will make up some test rear wing endplates to move the lower rear wing to our test positions.
So, for our initial test position, how about 0.5 wing chords rearward and 0.5 wing chords upward, from the end of the diffuser? By wing chord I mean the combined chord of the mainplane & flap.
Also, if the lower rear wing is now to be interacting with the floor, should we run it at a lower angle of attack to reduce the risk of separation?
Regards, Ian
#7
Posted 03 September 2008 - 16:03
Originally posted by cheapracer
Right;
I have a question based in logic but precious little knowlege of aero's.
In that (amazing NR and thanks) list there is a wing profile for a "human powered" wing. Now wouldn't that shape give the ultimate downforce for the slow speeds we are considering here?
You are talking about wings suitable for low Reynolds Numbers (i.e, slow speeds, at least compared to these of a North American P51 mustang fighter, and/or small dimensions).
Automotive wings are already studied for lowlish Reynolds , usually; any hillclimb car is anyway a hell of a lot faster than a pedal aircraft.
There are even profiles especially studied for model gliders, which experience even lower Reynolds numbers.
Aircraft wings are selected for Lift/Drag ratio, not just high (negative) lift.
Also, aircraft wings with too high moments (tendency to rotate around their chord axis) are not usually a good thing, while this could even be a benefit in a car.
So, I'd stick to automotive profiles.
#8
Posted 03 September 2008 - 19:22
Do you have suggestions on how to find the said automotive profiles?Originally posted by Paolo
So, I'd stick to automotive profiles.
#9
Posted 03 September 2008 - 20:59
Originally posted by Greg Locock
Milliken has some results from various cars which may give you some ideas for what an appropriate distance to move the wing is for each test.
Thanks for reminding me of that - Milliken references Katz which I've tracked down too. Seems like we might need the lower wing more forward than I expected, possibly even with an overlap...
You might want to think about 'reserving' one test so you can do a final run based on the results of the other 4.
If we put our engineering hats on we might find some value in a DOE, particularly if you start to worry about more factors, levels, or interactions. For instance in my work I often use first order interactions, and three levels for each factor. That'll need more than 4 runs, obviously.
(Late edit, well, no, recommendation for 4 runs, 2 factors at 3 levels is
Run Factor 1 Factor 2
1 M H
2 L M
3 H L
4 H H
for example, tho i haven't checked exactly what you'd get out of it. note that it is not balanced so analysis is not straightforward. Still that is fewer runs and more information)
We're not limited to 4 runs but need to limit total configurations to a manageable level. Once we have a candidate solution we do need to characterise it for aero balance and downforce at different ride heights and pitches.
I should have mentioned before that we have pressure tappings in the floor to indicate how hard it's working in the different configurations.
I'm not sure how wool tufts will work, did you mean use them to visualize the streamlines of the exit flow from the diffuser with the lower rear wing in the standard location? I guess that would be useful info in itself, although I don't know how to turn that data into a rough new position for the lower rear wing. Any ideas?Have you thought about a camera and wool tufts so you can at least figure out where the wing should be roughly?
Regards, Ian
#10
Posted 04 September 2008 - 00:07
Most augmentation on a F1 diffuser comes from the endplates with a chord washout on the beam wing.
Originally posted by murpia
I'm working on a project to increase the effectiveness of the aero package of a single-seat hillclimb car.
The idea is to reposition the lower rear wing elements to best interact with the floor and diffuser exit. The car has a flat floor (no step plane) with the diffuser starting at the front of the rear wheels. Currently the lower rear wing element is (probably) too high and too rearward to interact effectively with the floor.
Can anyone offer any advice or rules of thumb as to a good reference position to start from? Measurements based on wing chord and / or diffuser exit height would be best. We would like to limit ourselves to maybe 5 options to test: forward, backwards, higher and lower, from the reference position.
We plan to conduct a straightline aero test measuring pushrod loads to determine the best configuration.
Regards, Ian
#11
Posted 04 September 2008 - 00:24
Also, won't there be a strong interaction between angle of attack and location?
Incidentally, for a great example of KISS software have a look at http://www.microcfd.com/software.htm
It is only 2D. That is not a disadvantage.
#12
Posted 04 September 2008 - 03:32
Originally posted by murpia
Hi all,
Thanks for the great repsonses, so here's some more detailed info (it's alwayd hard to know where to pitch the initial post).
The car already has twin element upper and lower rear wings. Each wing is the same mainplane and flap profile, with a gurney. The wings have been extensively tested and flow-vizzed to set angles that are 'good' but 'safe' (i.e. low risk of separation).
Drag is not an issue - we know that more downforce will improve performance down to an L/D of about 1.0...
A more forward aero balance is what we expect from a better working floor, that goes along with previous results from fitting barge boards. Again this is OK, we can re-balance if needed with the front wing.
We have to use the existing rear wings, so the test is all about best positioning of what we have. As I stated before we believe the existing lower rear wing could be lower and more forward in order to 'activate' the floor better. We will make up some test rear wing endplates to move the lower rear wing to our test positions.
So, for our initial test position, how about 0.5 wing chords rearward and 0.5 wing chords upward, from the end of the diffuser? By wing chord I mean the combined chord of the mainplane & flap.
Also, if the lower rear wing is now to be interacting with the floor, should we run it at a lower angle of attack to reduce the risk of separation?
Regards, Ian
As far as your wing angles go, if you feel that you can see gains on the watch down to an L/D of maybe 1 (I agree, BTW), then why are you worried about separation? Dial some angle into it. Separation is not the same as operating in stall conditions. Separation just means that the wing is going to be a little less efficient than if it weren't. On these types of things, you need to keep a close eye on the stopwatch. If the watch likes it, then separation be damned.
Remember the pressure field on the airfoil in my previous post? Well, as you dial angle into it, the peak (negative) pressure will increase and near the tail of the foil, the pressure will come closer to static. As the wing starts to get separation, the tail end of the airfoil will see some positive pressure, but the peak pressure depression will still increase, at least initially, offsetting what the tail end of the foil sees. Use this to help your floor.
As far as gap goes, the chord you're really concerned with is the length of the car's floor + the rear wing in plan view, call it 'Floor Chord'. Not just the chord of the rear wing. We're essentially dealing with a slotted flap here, and so the floor of the car is the 'main' wing. The rear wing is the 'flap'. If it's got 2 elements, then it's a double slotted flap. The vertical gap between the main wing and flap will probably be about 2-4% of the floor chord. Ideally, there would be some longitudinal overlap between the diffuser exit and the rear wing. Most cars have rules that stop the floor at the axle centerline. If you don't have to deal with that, then bring the floor on back and overlap the rear wing 3-7% of the 'floor chord'.
These are pretty rough numbers, I know. Sorry 'bout that, but aerodynamics is a tricky thing, and it's really, really tough to engineer it from a book. Ultimately, you have to go do real tests. Ultimately, it wouldn't surprise me in the least if you came up with good numbers that were completely different from what I recommend. There's just so much going on at the back of any racecar that any of this type of advice is going to involve a fair bit of hand-waving. Please, salt to taste on everything I've written here.
#13
Posted 04 September 2008 - 12:08
Originally posted by Lembit
Do you have suggestions on how to find the said automotive profiles?
Some are drawn on
"Wings" by Enrico Benzing, Giorgio Nada Editore.
No polars, unluckily, but you can take the wing sections from there.
Polars change when wing is installed, anyway...
Also have a Google search for Liebeck banana wing profile.
#14
Posted 04 September 2008 - 21:08
Originally posted by Fat Boy
As far as gap goes, the chord you're really concerned with is the length of the car's floor + the rear wing in plan view, call it 'Floor Chord'. Not just the chord of the rear wing. We're essentially dealing with a slotted flap here, and so the floor of the car is the 'main' wing. The rear wing is the 'flap'. If it's got 2 elements, then it's a double slotted flap. The vertical gap between the main wing and flap will probably be about 2-4% of the floor chord. Ideally, there would be some longitudinal overlap between the diffuser exit and the rear wing. Most cars have rules that stop the floor at the axle centerline. If you don't have to deal with that, then bring the floor on back and overlap the rear wing 3-7% of the 'floor chord'.
We can't bring the floor back any further, but it's already back beyond the rear wheels.
Here's a rough sketch of the current relative positions of the rear wheels, rear wings and floor / diffuser. We think the upper and lower wings are a bit too close together:

And here's roughly what we plan to try, we'll base the exact new position of the lower wing on the 'floor chord' idea:

Comments appreciated,
Regards, Ian
#15
Posted 05 September 2008 - 03:02
Good luck.
#16
Posted 05 September 2008 - 03:59
#17
Posted 05 September 2008 - 09:46
The Guy uses "Cosmosfloworks"
Go to post 53
http://www.productde...opic=7699&st=45
Also from memory the Stohl F1000 racecar may interest you in that area of their design if you can find some pics.
#18
Posted 05 September 2008 - 11:42

#19
Posted 05 September 2008 - 12:43
Originally posted by cheapracer
Ian i don't know if this is of any help....
The Guy uses "Cosmosfloworks"
Go to post 53
http://www.productde...opic=7699&st=45
Also from memory the Stohl F1000 racecar may interest you in that area of their design if you can find some pics.
Sorry only registered uses can access images.
You're welcome re foil database, there are naturally a lot more than that small list. NACA had one ages ago, but it has gone AWOL.
hillclimb car in UK and Australia is essentially a low speed event...europe is very very different:
http://www.youtube.c...feature=related
Advertisement
#20
Posted 05 September 2008 - 17:11
http://www.productde...act=Reg&CODE=00
...and ur right, I was thinking in Oz climb mindset.
#21
Posted 05 September 2008 - 17:31
Originally posted by Greg Locock
figure 6-71 in Katz (which I coincidentally received this morning) is relevant - showing how a rear wing modifies the pressure distribution all the way along the floor of a ground effect car with a diffuser.
The 1995 edition, doesn't. Damn, I suppose I have to buy another.
#22
Posted 05 September 2008 - 17:38
I'd like to genuinely thank everyone involved.
#23
Posted 05 September 2008 - 19:14
Just you wait until I post some actual results!Originally posted by Fat Boy
Color me amazed by the civility and usefulness of this thread. It seems that most threads on this board turn brown and run downhill after about 10 posts. This one is still shiny after 20.
I'd like to genuinely thank everyone involved.
Hopefully the test will occur next Thursday, UK weather permitting...
Regards, Ian
#24
Posted 05 September 2008 - 20:31
Originally posted by murpia
UK weather permitting...
Regards, Ian
Ya, well, I guess I won't hold my breath!
Have you done coastdown testing before?
#25
Posted 05 September 2008 - 20:52
Yes I have personally, but we won't do any this time as the clutch & crankshaft thrust bearings on the car aren't up to it. Anyway we know that drag is not an issue for this car and the type of venues it runs at.Originally posted by Fat Boy
Have you done coastdown testing before?
Logging wise we have pitot-static pressure, 10Hz GPS velocity, pushrod loadcells, laser rideheights and damper pots. The car has a monoshock front and 3rd spring rear and we adjust the packers on those to get the rideheights we want. Test procedure is a low speed 'roll' to get zeroes for the loadcells, followed by a 'ramp' (a slow acceleration from the roll up to 100mph), followed by 2 constant speed sections of 100mph in opposite directions to account for wind.
The ramp allows quick'n'dirty downforce & balance numbers to be generated by a scatterplot linear regression of pushrod load vs. pitot pressure. Post-processing the data to remove the low speed 'roll' offsets usually gives lightly more accurate final numbers, valid for the rideheights achieved during the constant speed sections.
GPS speed vs. pitot allows us to calculate air density for each run.
Regards, Ian
#26
Posted 05 September 2008 - 23:48
#27
Posted 06 September 2008 - 02:30
http://www.racemagaz...&id=41&Itemid=1
Can I assume you are using an relatively new Gould or some such?
#28
Posted 06 September 2008 - 02:35
Originally posted by cheapracer
NR that design forum is public, just register (very simple) - a very interesting forum too.
http://www.productde...act=Reg&CODE=00
...and ur right, I was thinking in Oz climb mindset.
Ok, will have a look.
Frankly I think some of the european hillclimbers are insane. There was footage of an F3 car flat in 6th for 15seconds though a french forest with no road side barriers and just trees rushing past.
In one of the vids I posted you can see the sparks when the rear wheel hits to barrier at speed in a high speed! It does show that these international events are run under FIA rules that are read in a different manner to locally.
#29
Posted 06 September 2008 - 13:59
Don't you just love to see rod-ends in bending on a big, powerful, high-downforce racecar...Originally posted by NRoshier
May not be hugely helpful, but I posted a new article on a much modified F300 lola used on the hills in Australia.
http://www.racemagaz...&id=41&Itemid=1
Can I assume you are using an relatively new Gould or some such?
Regards, Ian
#30
Posted 06 September 2008 - 14:11
I was just thinking that you might need to adjust something at the front / sides of the car as well for one of your runs.
#31
Posted 06 September 2008 - 17:46
Originally posted by murpia
Don't you just love to see rod-ends in bending on a big, powerful, high-downforce racecar...
Regards, Ian
Much less of a deal than an FSAE judge might obsess about.
#32
Posted 06 September 2008 - 19:42
What about installation stiffness?Originally posted by Fat Boy
Much less of a deal than an FSAE judge might obsess about.
Regards, Ian
#33
Posted 06 September 2008 - 19:55
In the dark ages, one of my early FSAE cars got ripped for doing just this. The next year we made damn sure we had monoballs everywhere. Did it look cleaner, yes. Did it make the car perform any better, not really.
As a design judge, I've had other design judges act like by having a rod end as an upper ball joint the car is going to explode. They've never spent time in a race paddock and have no idea how common it is to see in really good cars (the Riley DP, for instance, seems to get through a 24 hour race OK). I just ask the students to justify what they've done. If they have numbers to justify what they've done, then I'm OK with it.
#34
Posted 07 September 2008 - 00:42
However the next time you are cursing the taper on one of those, think about how huge the thing is compared with a typical spherical joint. It's only taking a ton of load.
#35
Posted 07 September 2008 - 23:04
Ian, as fatboy said it is not perfect, but it is practical. As I noted a while back, Australian Hill Climbs are relatively low speed, so the loads will not be too high.
#36
Posted 25 September 2008 - 20:28
Testing went smoothly, of course you never have enough time to try everything, but the weather was good with very little wind.
We couldn't improve on the current configuration:

We tried a number of variants of the test configuration:

The best was found to be with the leading edge of the lower rear wing in line with the trailing edge of the floor, with a vertical gap of about 40mm. We think we have 2 effects at work here: moving the rear wing down may have helped the floor & diffuser, but it has lost some of it's own downforce by being more shielded from clean air by the bodywork. We increased the angle of attack of both wings in stages until we saw no further improvement, but the total was still worse than before.
We may try the following if we get another chance:

The idea is to keep the current rear wing performance but work the floor & diffuser harder.
Also, we will try similar increases of angle of attack of the current wing configuration, and see if it responds like the repositioned wings.
Comments?
Regards, Ian
#37
Posted 26 September 2008 - 16:00
Here is another thought, which is complete speculation. The diffuser isn't at it's limit, so it doesn't need help from the rear wing to keep the flow attached. If it needed help from the wing to keep the flow attached, then you may very well have seen some gains, but as it is, the loss in flow to the rear wing more than offsets anything you might get out of the undertray. Of course, this is pretty much what you said.
#38
Posted 27 September 2008 - 04:09
What is the area like prior to the lower wing?
#39
Posted 27 September 2008 - 20:59
Originally posted by NRoshier
I've been looking at helping a friend with his F2 car to make it better on the hills. At the rear I've been wondering about the wheel turbulence post wheel and also separating the wheel from the deck area between the wheels.
Remember the snorkel rear brake ducts for Champ cars? They had little to do with brake cooling, and a lot to do with shielding the rear wing from nasty air off the tire. I heard that at one point a team was going through tech and they had the snorkels on, but completely taped off. The tech official said that if the snorkels were completely taped off they'd have to take the off the car because they were no longer brake ducts. Without saying a word, the engineer grabbed a pencil off his ear, poked a hole through the tape, and then asked, "Are there any other issues?"
Advertisement
#40
Posted 28 September 2008 - 04:05