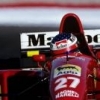
Designing and building my own engine...
#1
Posted 03 December 2003 - 23:15
Air cooled Flat-6 using aftermarket billet aluminum cylinders from http://www.lnenginee...om/nickies.html bore size approx 106.3mm
to reduce engine width as much as possible for optimal packaging and underbody aerodynamics, I'm gonna go with a scotch-yoke setup similar to this: http://www.cmcpower..../howitworks.asp which also has the side benefit of making the engine shorter, lighter, and more mechanically efficient due to reduced piston side forces. The scotch yokes will either be welded up or CNCed from 4340 steel.
Crank will also be built up from welded 4340 rod and plate, unless you guys can point me to a better alternative (and no, I don't feel like paying $2k+ for a billet crank). Stroke will be ~78mm for a piston speed of 4200fpm @ 8000rpms, should I want to rev that high. Crankcase will be machined out of 6xxx aluminum. I'm thinking studs are better than bolts, and I'm thinking of employing a "thru-stud" to connect the heads to the crankcases... Remember, with a scotch yoke layout, there need not be any cylinder bank offset. Fasteners were never my strong point, so I would appreciate some input here. Pistons will be machined Al billets. I remember once reading that in the presence of a strong vaccum in the crankcase, one can do away with the oil-control ring... Is there any truth to that? I will be employing dry-sump lubrication and I would welcome any opportunity to minimize piston/ring friction...
Now we come to valvetrain and heads, I can either go with aftermarket 2V/cyl VW heads, which would automatically mean the use of pushrods and cam in block construction see this link: http://www.scatvw.co...inderheads.html , or I can CNC/weld my own heads, a difficult endeavor at best... If I do decide to go that route, I'd probably stick with 2valves/cyl, but I'd probably go with twin plugs, as well as a modified version of Michael May's fireball head, to enable 13:1+ compression ratios... check this link out http://www.theoldone...Soft_Head_1999/
I still haven't decided if I want to go with pushrods or SOHC, and if I do go with SOHC, whether I want direct acting cams or finger followers... It all depends on time & $$
That's all I can think of for now, its 1am and I'm sleepy... I'd love to hear your comments on everything, as well as constructive feedback. I'm just wondering, would I need a balancer shaft for engine balance? The way I see it I don't think so... Hope to hear from you soon
Advertisement
#2
Posted 04 December 2003 - 00:30
If you really want a light, compact NA engine with around 400 hp, try to find an old DTM engine. For example we have the Cosworth Opel engine, 2.5 liter V6 with 450 hp @ 11,000 rpm and a weight of little under 90 kg.
#3
Posted 04 December 2003 - 05:57
#4
Posted 04 December 2003 - 07:59
Quote
Originally posted by Earthling
Besides, how long do you seriously expect your Opel engine to last between rebuilts?
Possibly a bit longer than one with a welded crank...... Where are you going to race this thing? I want to be a long way away when you give it full throttle. Buy the billet crank.... you know it makes sense.
#5
Posted 04 December 2003 - 13:45
or just buy the porsche engine,
unless you have access to all of the materials you listed and unlimited machine time (on the right machines) for free, and don't mind spending a few years machinging parts.
Billet pistons??? what? you can get good pistons made to your specs, try that first
Why the scotch yoke? what are the benefits? (why hasn't anyone used one in the last 100 years?)
I hate to be negative, but I can't believe you are at all serious about this.
JwS
#6
Posted 04 December 2003 - 17:29
Quote
Originally posted by Earthling
a medium-large displacement Flat-6.
Air cooled Flat-6 using aftermarket billet aluminum cylinders
to reduce engine width as much as possible for optimal packaging and underbody aerodynamics,
The scotch yokes will either be welded up or CNCed from 4340 steel.
Crank will also be built up from welded 4340 rod and plate, unless you guys can point me to a better alternative (and no, I don't feel like paying $2k+ for a billet crank).
Crankcase will be machined out of 6xxx aluminum.
I'm thinking studs are better than bolts, and I'm thinking of employing a "thru-stud" to connect the heads to the crankcases... Remember, with a scotch yoke layout, there need not be any cylinder bank offset.
Pistons will be machined Al billets.
which would automatically mean the use of pushrods and cam in block construction
I'd probably stick with 2valves/cyl.....I still haven't decided if I want to go with pushrods or SOHC, and if I do go with SOHC, whether I want direct acting cams or finger followers... It all depends on time & $$
Hhmmm. Well, you're using waay too much billet.....how long do you want this engine to last? Lose the billet piston, billet crankcase, and billet crankshaft if you can. Go with forged components.....more expensive, yes, but far better material selection for the application. Of course, if the engine isn't supposed to last a long time or has a short period between overhauls, then billet is fine.
Welded/assembled crank? Bad idea, man....unless you like tearing the engine down after every run and rebuilding the crank. Ugh.
Studs and bolts are pretty much the same.....threaded material. Just make sure you use threaded components whose threads are ROLLED rather than cut threads.
Why would you spend the time and effort building your engine and go with 2 valve SOHC? 4 valve DOHC is the way to go.
Sounds like you need to layout what your requirements are and then design the engine to suit. 2 plugs per cyl, but 2 valves? Huh? Sounds kind of helter-skelter to me.
Oh yes....what kind of underbody aero are you thinking of? Lateral flat-6 engine isn't the best way to go for certain undertray configurations.
Need.....more......data.......
#7
Posted 04 December 2003 - 18:26
Quote
Originally posted by Earthling
You can pic up a slightly used dry-sump pump for literally a couple hundred bucks from sprint car racers, so its not that big a deal. Besides, I would think a dry sump would be necessary for a car able to pull over 1.3g's lat accel. Besides, how long do you seriously expect your Opel engine to last between rebuilts?
Those pumps are cheap for a reason, people are afraid from buying them since if they are damaged, which can be hard to tell, they can destroy the engine.
I expect that the Opel engine will last much longer than your welded crank will. That engine will also have the right manufacturing processes on it's parts; for example billet are not used for pistons (except prototypes) since it give poor reliability.
Furthermore, the cylinderhead(s) is the most important part of the whole engine when you want a high power output. To spend a lot of money on an engine and then chose an old two valve design doesn't sound that smart. If you compare it to the Opel engine which have a modern 4 valve head design, it's even possibly that it uses a pneumatic valve system, it will need a larger displacement and this will make the engine heavier. A NA 400 hp, below 100 kg engine isn't that easy to design and manufacture.
#8
Posted 04 December 2003 - 19:13
Do your rules dictate N/A?. It would be much easier to meet the 100kg limit if you look at blown motors.
Lightweight, high horsepower, durability, low cost - choose two because you cannot choose all four.
#9
Posted 04 December 2003 - 19:31
Getting a VW engine up to 400bhp would entail a specific output of at least 200bhp/L , which no matter what you do, is gonna cost a fat wad of cash, not to mention result in appaling longevity, and you'll still be stuck with its inherent design flaws. A half-decent (complete) Porsche engine will cost in the high four figures, and that's before modifications, which are pretty damn expensive to say the least. I happen to be lucky enough to have access to a large automotive machine shop, as well as a CNC machine. Besides, I can outsource whatever I can't fabricate locally to any number of companies in Europe and North America. Believe me, I've very seriously considered using/modifying an existing design, but there are just too many compromises involved. Furthermore I've been dreaming of designing my own engine since I was 13, and since I'm a mechanical engineer by training, I figured now's a good a time as ever. So as you can see my heart's pretty set on this, and its not a question of if, but a question of how.
With that out of the way, by welding the crank, I meant building it up, like old VW/Porsche cranks, and certain motorbike cranks, my bad there... Although I am currently looking into going the billet route. As for the scotch yoke concept, I really have no idea why it hasn't been used, although the fact that it was patented in '89, or was it '92 I forget... probably has something to do with it. You can find a list of the advantages, in addition to a host of excellent tech papers at
http://www.cmcpower..../advantages.asp and
http://www.cmcpower..../techpapers.asp
I strongly urge you gentlemen to check it out... Now with that out of the way, what do you guys think?
#10
Posted 04 December 2003 - 20:07
Quote
So as you can see my heart's pretty set on this, and its not a question of if, but a question of how
Not too many souls are brave enough to attempt what you want to try. I'd say it's not a question of how, but a question of how much money.


Building your own motor is not a cheap or easy undertaking. Starting from scratch and aiming at 400HP and 100kg may be bordering on the impossible if you want to keep your budget under $100K. Prototypes and development are very expensive, very quickly.
Buying and modifying the Porsche motor is going to be cheap in comparison to what you are attempting. But I wish you the best of luck.
I'd be looking at the Import drag racers in the states. Some of those are approaching 250HP/liter, longevity not being a concern. Or something blown. 450HP from a stock 2.5liter Subie motor with only intake, exhaust, fuel management, and boost mods. No internals. Guessing close to your 100kg limit, but just guessing. Or buy an existing race motor. Plenty meet your requirement, but they may not meet your budget.
#11
Posted 04 December 2003 - 20:35
I guess I wasn't being too clear on the pistons, they will be forged 2618 (RR58) and (custom) machined... I guess I've been reading too much company literature. What's wrong with a billet crankcase? Surely it can't be any worse than a cast crankcase for God's sake. And as for these 400bhp SCAT engines everybody keeps telling me about, a quick google search for 400bhp SCAT VW turned up one and only one hit, which was unrelated anyway... Again, we're talking about well over 200bhp/L, which means we're probably talking about (some very expensive) forced-induction. I'd like to keep it NA in the interests of throttle response, and packaging and durability reasons.
As for pushrods and 2v/cyl, I believe that 4v/cyl is overkill for all but very high-end applications, we've discussed this on the TF before, check this link out: http://forums.atlasf...y=&pagenumber=2
Just look at the Chevy LS1/6 which can get up to 100bhp/L with a bit of modification, or NASCAR engines, which get 125bhp/L using 1 old-school carb and no electronic controls. All those extra valves and cams and belts cost money you know, plus its just more s**t to go wrong. I'll probably be going with pushrods, so I'd be using aftermarket Chevy parts... Tried and tested technology, and won't break the bank either.
I am well aware that this isn't an easy undertaking, but $100,000 puh-lease! As I said, most of the machining costs are essentially free, and labour is pretty cheap where I'm at, so I had figured a budget of around $6k for materials, outsourced components, and miscellania. Its not like I'll be DEVELOPING my own bearings or roller lifters... I'd like to think of it as a hybridized Porschevy engine with a bit of extra sugar and spice... Subie motor with all the mods would end up costing around the same, and its still a turbo
#12
Posted 04 December 2003 - 20:49
Quote
Originally posted by Earthling
I guess I wasn't being too clear on the pistons, they will be forged 2618 (RR58) and (custom) machined...
What's wrong with a billet crankcase? Surely it can't be any worse than a cast crankcase for God's sake.
As for pushrods and 2v/cyl, I believe that 4v/cyl is overkill for all but very high-end applications,
All those extra valves and cams and belts cost money you know, plus its just more s**t to go wrong. I'll probably be going with pushrods, so I'd be using aftermarket Chevy parts... Tried and tested technology, and won't break the bank either.
Glad to hear the pistons are forged!
As far as the crankcase.....I guess it depends on how highly stressed thje crankcase is, and how long you want it to last. If it's lightly loaded....no problem. If it's highly loaded, there is a high probability that the billet will fail in fatigue. 'Tis the nature of billet, my man. Castings are a bit better....the grains are at least equiaxed, as opposed to rolled billet, which generally has "stretched" or "flattened" grains. Forging would be best, but might be overkill depending on how your engine will be loaded.
How is 4 valves per cyl "high end?" My Saturn SL2, made as an entry level compact, had 4 valves per cylinder....with a timing chain, no less. Yes, it was a 4 cyl, so only 1 camshaft for each valve bank, and only 1 chain......but you claim to be worried about throttle response. How is all the parts and lash of a pushrod arrangement going to improve throttle response of a 2 valve per cyl engine? Huh? The SL2 engine had like 40 HP on the SOHC version of the engine......
And how is a simpler, less part-intensive OHV setup not "tried and true?" My thought is that people are biased to the Chevy pushrod arrangement because there are so many aftermarket parts available, and because many of the parts are interchangeable between different engine models. You're making a custom.....why not go with the proven OHV setup, get the HP and response benefits? Use timing chains or a gear system......in the end it will be less parts than the pushrod system, easier to repair and adjust, and you'll be able to get better HP and throttle response. Hell, rape a Saturn engine for the heads.....
I'm not sure how you're making a "custom" engine when you're limiting yourself to old pushrod technology.......do you want a fire breathing total custom, or are you making "Franken-engine?"
I'm still not too sure what you're getting at......do you just want to make the block and crankshaft, and then recycle the rest? Why do that? How is that custom? Why not rebore and reline an existing block........
I still need more data.....
#13
Posted 04 December 2003 - 21:49
Quote
a quick google search for 400bhp SCAT VW turned up one and only one hit, which was unrelated anyway
Read my earlier post
Quote
A SCAT motor is half of a chevy small block V8, highly developed for sprint cars. Competitive unit costs $25K.
a SCAT motor is NOT a VW. I think you are getting confused with a California company (maybe called SCAT motors or similar) who makes a lot of parts for VW's used in sandrails and the like. A SCAT motor is based of a SBC block but cut in half. They may have originally been built for Midgets, a type of sprint car.
Even with maching being free, and labor being almost free you are dreaming if you think you are going to build a motor from scratch for $6K. I don't think you fully grasp the amount of design and machine work that goes into a complete engine. And you are expecting a brand new unproven design to be reliable? Out of the box? How?
Now a "franken" motor, maybe. $6K will build you a small block chevy capable of over 450HP, add another $2K for a dry sump. But double your weight limit.
Good luck though, keep us informed of your progress.
#14
Posted 05 December 2003 - 12:09
There have been some people building V8s based on Yamaha barrells and heads, making their own crankshaft and crankcase.
You could make it a flat-8 if you so desire.
btw, haven't scotch yokes been around (in theory) for 100 years?
#15
Posted 05 December 2003 - 13:12
Use rolled threads on fasteners, and even though I'm a through and through metric man, seriously consider using Whitworth or BSF threads rather than metric or UNC / UNF where highly loaded studs are installed in aluminium casings, i.e. for main bearing caps.
I'd get a copy of a mechanical design textbook (anything by Lipson / Juvinall / Norton / Shigley) and a copy of Stress Concentration factors by Peterson will be pretty educational. This way you can design out a lot of potential mistakes.
I'd echo the sentiment about using motorbike top ends. Cheap, plentiful, light and tried and tested. I think the Kawasaki motoGP bike uses machined crankcases.
Just to be controversial..... at least one former championship-winning F1 manufacturer has used machined-from-solid pistons in the last few years in Grands Prix. Not forgings.... machined from solid billet.
That's it, I'm going to get a sarnie

#16
Posted 05 December 2003 - 13:27
Old Porsche cranks were built up using a unique radially splined and threaded connection (Hirth differential threads I think) which worked well, but required very precise machining. The only reason for this was that they had roller bearings for the mains and rod big ends (the only reason for that was the poor state of journal bearing tech at that time). Motorcycles abandoned the built up crank (on multicylinder) in the 70's when they started to make real power (nowhere near what they make now). They were pressed together with tremendous interference and still would barely hold, welding helped but not enough. I think the last was the Kawi Z1
Scotch yokes were used extensively on steam engines, do a little research on conventional journal bearings and the loading situation of the crank.
Yes, good cyl heads!!! you could look at ducati 4v heads??
JwS
#17
Posted 05 December 2003 - 14:05
Using somebody else's cylinder head would make sense.
I think Hyabusa 1300s are making 170hp from the factory now. I'm sure there is plenty of tuning bits for them, cams, valves, etc, that can lift that over 200hp. If you have what is basically 2 of them, you'd go close to your 400hp.
I would think that the 100kg weight limit is going to be pretty tough to achieve, whichever way you go.
#18
Posted 05 December 2003 - 16:59
I know about 3 different manufactors, Motopower "firehawk RST 2.0 litre V8"
Cyclone "power y40R 2.0 litre V8" www.cyclonepowerltd.co.uk
and Maxsym "Radical 2.6 litre V8" www.maxsym.com
www.PowertecRacing.com builds Radicals motorcycle engines and maybe they could modify an Honda goldwing flat 6 to produce the figures that you want?
Or you have the TVR AJPV8 4.5 liter 460hp and 125 kg V8 for good money seen in the Tuscan race car.
#19
Posted 05 December 2003 - 17:39
The Scat heads that you are looking at are not acceptable for what you are looking for. They leak, the pushrod geometry is all wrong for an aircooled engine, Scat even says that they are not the best design. In order to get 400hp out of a T1 Aircooled VW motor you will be doing a lot of work and better come up with a better crankcase. A T4 with a set of aftermarket heads could be configured to make that number but you will have to come up with a better set of heads.
I don't have problem with the Porsche 6 cylinder engine, it is extremely durably. Not very economical, and the power levels are kinda disappointing in NA form but it could be great for a kit car or some other sort of homebuilt street or race car.
The SCAT v4 is for race use only. It has it's own problems that you need to research. I am designing an engine right now and I am planning on going the Honda head route, they have excellent heads and they are very easy to source. There is a huge aftermarket and developement work has been pretty intense on Honda engines so parts would be cheap.
Dropping 2 grand on a crankshaft makes good sense if you can't find the one you need from some sort of production vehicle. You will be spending a large chunk of change on this engine but 100k seems a little outrageous. 15-20k would not suprise me in the least, although with you doing a lot of the machine work your price can be kept fairly reasaonable.
Good luck with it and keep us posted.
Advertisement
#20
Posted 05 December 2003 - 19:12
As for the issue of heads, you're absolutely right, it makes much more sense for me at this point to use an existing head design. Since I'm probably gonna go with a 4 head bolt design, I'm limited to using either Gen III LS1/6 heads, or aftermarket aluminum Small Block Ford heads on account of the 4.4" bore spacing, of course I would have to chop off a quarter of the head to use it with a 6 cylinder engine, which would mean I would have to play with the water passages a bit to make sure everything is leakproof. Its either that or switch to a 5 head bolt pattern and use aftermarket aluminum chevy/buick V6 heads. Motorbike/Honduh/etc heads would be nice, but they're pretty expensive. a couple of top of the line small block heads with all the bells and whistles run up to $1200. Besides motorbike/honda heads wouldn't have the necessary bore spacing needed. Remember, I'm running 106.3" pistons, which brings us back to the whole "big-block 6" issue.
Based on preliminary sketches, a cam in block/pushrod arrangement is difficult at best, so I was thinking of running the camshafts in the valve covers (!) which would have to be custom, billet items, its either that or doing some pretty crazy mods to the heads... Comments, ideas anyone?
As for built-in stresses from machining, I wasn't familiar with that... Interesting point, got any good references or links you could direct me to? I'm guessing I can get around the problem by doing my preliminary machining, subject everything to a few heat cycles, before doing final machining. How large are these residual stresses anyway? Btw, is 6xxx Al good enough for block and crankcase, or should I go with 2xxx or 7xxx?
Finally there's the issue of scotch yoke design. Check this paper out: http://www.cmcpower....other/sae97.pdf
Looks pretty good to me. You're right about the bending loads on the big end of the yoke, I guess that's just something I'm going to have to design for and live with, unless you see something I don't...
Keep em coming guys!
#21
Posted 05 December 2003 - 22:47
This will give you improved torque at lower revs, if done well.
For example:
A standard Hayabusa engine has a bore of 81mm and a stroke of 63mm, for 1300cc.
Making a V8 with the standard bore/dimension would obviously yield 2600cc.
Increasing the stroke to about 72.5 would yield approx 3000cc, and making the bore/stroke ratio 1:1 will give 3300cc approx.
And I'm sure you can bore the Hayabusa engine bigger than the 81mm, but I'm not sure how far.
#22
Posted 05 December 2003 - 23:46
Apparently the original centre to centre distance of the cylinders was 88mm, with the standard 81mm bore. TTS wanted bigger bores, so they built a new block with a bore spacing of 93.5mm, and have a new bore of 91mm. The crank has been stroked up to 73.5mm, which gives an all up capacity of 1912cc. The bores don't line up with the combustion chambers, so the pistons all have different valve cut outs!
They are claiming approx 270hp from 9000-10500rpm. Torque is 180ft.lb from 6000-7500rpm.
The new engine block is machined from a solid block of Aluminium alloy HE30 (6082).
I would think that there would be some capacity for increasing the bore without going to such extremes!
#23
Posted 05 December 2003 - 23:48
#24
Posted 05 December 2003 - 23:55
Quote
Originally posted by Earthling
This way I get to have my cake AND eat it... Low C of G without disturbing underbody airflow... what more could you ask for?
Where are you going to put the exhausts?
What class of car is it going in? Is it mid engined/front engined?
Quote
Originally posted by Earthling
Its either that or switch to a 5 head bolt pattern and use aftermarket aluminum chevy/buick V6 heads.
Would the Buick/Chevy V6 have the necessary bore spacing?
#25
Posted 06 December 2003 - 00:02
Pretty much all of the old school small-blocks and their derivatives have a 4.4" bore spacing. Same goes for the Gen III chevy small block... Pretty cool huh?
I'd really appreciate it if we could have a real-time discussion on MSN or AOL or whatever, my email addy for MSN is hydra@caltech.edu, and my AOL screenname is PowerOversteer.
Wuzak, Halfwitt & co, I'm waiting to hear from you all!
#26
Posted 06 December 2003 - 00:18
#27
Posted 06 December 2003 - 00:31
#28
Posted 06 December 2003 - 01:38
Quote
Originally posted by Wuzak
Where are you going to put the exhausts?
The exhaust are going to give problems. Because of the exhausts the engine can't be placed that close to the ground, and a large portion of the weight will be placed out from the center of the car. This cancel out the low cog of a boxer engine. But that's probably why we don't see any boxers in F1 today.
Today there are motorcycle engines using up to around 15,000 rpm, so durability at high speeds can be solved. One of those engines would probably have a durability no worse than a tuned american V8 engine, even though they are using much lower revs.
Making a V8 engine out of two MC engine like Hayabusa or R1 should probably meet the requirements of 400 hp and a weight below 100 kg.
#29
Posted 06 December 2003 - 19:46
Quote
Originally posted by Earthling
Hello all, its me again... After a lot of thought I've decided that modding a Subaru EG33 Flat-6 is too much work for not that much return (and a lot of $$),
I've just come to this late.
Are yousaying you were worried about modding an existing engine costing too much, so you're building your own from scratch?
That's the sort of inverse logic I'd expect from a politician :-)
Ben
#30
Posted 07 December 2003 - 11:45
http://dot.etec.wwu....30/v30pics.html
http://fsae.com/6/ub...4511#3626054511
http://fsae.com/6/ub...4373#7606084373
Western Washington University an FSAE team, designed and built there own V8:
'The V8 engine and 6-speed transmission on Viking XXX are two items that make this car stand out. The engine block, crankshaft, connecting rods, and transmission case were designed and manufactured at the VRI by the FSAE team. The engine block was CNC machined out of aluminum. The heads were taken from a Kawasaki 250cc 4-stroke motorcycle engine that made peak power at 19,500 RPM. The 6-speed transmission case was machined in house out of aluminum, and features internals borrowed from a Honda 600cc F1 motorcycle. The transmission and engine are fully stressed members of the chassis and feature mounting points for the suspension.'
taken from
http://dot.etec.wwu....ae/viking30.htm
#31
Posted 07 December 2003 - 13:04
Have there been higher rpm tests elsewhere? After all, you are talking about running 8000rpm.
#32
Posted 07 December 2003 - 13:30
Quote
Originally posted by dancin stu
you might want to check out these websites:
http://dot.etec.wwu....30/v30pics.html
http://fsae.com/6/ub...4511#3626054511
http://fsae.com/6/ub...4373#7606084373
Western Washington University an FSAE team, designed and built there own V8:
'The V8 engine and 6-speed transmission on Viking XXX are two items that make this car stand out. The engine block, crankshaft, connecting rods, and transmission case were designed and manufactured at the VRI by the FSAE team. The engine block was CNC machined out of aluminum. The heads were taken from a Kawasaki 250cc 4-stroke motorcycle engine that made peak power at 19,500 RPM. The 6-speed transmission case was machined in house out of aluminum, and features internals borrowed from a Honda 600cc F1 motorcycle. The transmission and engine are fully stressed members of the chassis and feature mounting points for the suspension.'
taken from
http://dot.etec.wwu....ae/viking30.htm
Nice looking engine.

One head is driven off the front of the engine, and the other off the rear. That is the logical, and easiest way to do it. Saves mucking around trying to get them to both drive off the front. Needs new camshafts on one bank (?), but you'd probably get new cams anyway.
Engine in Bits
Also, doing some research on motorbike big bore kits last night, and it seems you can stretch a Hayabusa to 85mm bore, which would give you 2860cc for a V8 version using the standard stroke (63mm). Should be able to get the 400hp from that.
The older GSXR1100s can be stretched to 86mm/87mm bores. They are also air/oil cooled, with their camshafts driven off the centre of the crank.
#33
Posted 07 December 2003 - 14:15
If you're determined to go the pushrod/two-valve route (ouch), you're going to need the best "3-cylinder" heads available... The splayed-valve Bow Tie V6/90 head, PN 10134394 from Chevrolet. Designed for 4.125" bore and 4.4" bore centers. Seriously good port flow as purchased. And they're aluminum, only 14 lbs. each bare. And piston crowns have already been optimized to match their chambers and valve clearance. Unlike "all" other small block "wedge" heads, these have the intake valve tilted 16° to the deck and 4° to the crank, and the exhaust valve tilted 11° to the deck and 4° to the crank. The 4° splay makes the valves move toward the center of the bore as they open, unshrouding them from the cylinder wall.
Now here comes the neat part... Chevrolet has an unmachined heavy duty crankshaft PN 14044838 that is forged from vacuum degassed 5140 and has three common rod journals (i.e. two rods share a straight journal rather than the offset journals of the production cranks). The common journal makes this an odd-fire competition crank with the 90° VEE, but... tah-dah... makes it a perfect crank for a 120° V6. The crank maker of your choice can turn this raw forging into a crank with a finished stroke of 3.25" to 3.75" (yielding 4.3L to 4.9L with the 4.125" bore) ... and of course, being also designed for the same engine as the aforementioned heads, shares the 4.4" bore center spacing. The end cost of a crank made from this forging will be less than half of what a custom billet crank would be, and since it is so similar to the SBC crank, they can apply all their well proven mass reduction tricks to it.
As for pedigree, as I recall these heads and crank were used to make over 900HP (seriously boosted) in the Goodwrench Corvette GTP (a re-bodied Lola) that blistered the track leading the 24 Hours of Daytona for several hours.
Custom billet cams are also expensive. Early Chevy V6/90 engines were semi-even-fire as a result of offset ground (by 18°) crank journals... later ones were true even-fire by way of further offset ground (30°) crank journals. So the cam for the later engine can be used for your even firing engine, but since you've changed the VEE angle (and therefore the angle the pushrods approach it) it can only be used for one bank... and another one for the opposite bank. So you have a "twin-cam-in-the-Vee" engine. As long as you have to use two cams, you might as well move them up closer to the head to run shorter pushrods. The high performance even-fire cams are PN 10051165 (hyd flat tappet) and PN 10134321 (hyd roller tappet), but these same cores could be reground to different specs if necessary.
You'll have to forget the air-cooled cylinders (thankfully... $3000 for six of the 106mm!) as I don't think you can get them crowded to 4.4" bore centers and have equal cooling for the center one. For a one-off engine, make the crankcase separate from the water-cooled cylinder blocks, like many motorcycle engines, and the V8 derivatives of them (I saw the MotoPower/Yamaha 2L 40-valveV8 up close and personal yesterday at PRI in Indy... tiny, pretty, and SWEEEET!).
#34
Posted 07 December 2003 - 16:26
As for the heads, the bow-tie heads look really neat, however, they've got a 5-bolt head pattern, whereas I would have preferred 4-bolt, but more importantly, they're $1300 EACH

After doing a bit of searching on google and Sallee Chevrolet, your crank PN is nowhere to be found... So I guess that leaves me with 2 options; go with a billet crank, or use a stock cast 4.3L GM crank with 30 degree offset crankpins, weld up the journals using a submerged-arc process, and offset grind the journals for the desired stroke and big end diameter... Does that sound shady to you? What do you think?

As for cam(s), it doesn't have to be 100% billet, you can go to any reputable cam company like compcams, crane etc and order a cam with any combination of (pre-designed) lobe, cam journal diameter etc... and its only $300-400...
I've ditched the idea of air-cooled cylinders a while back. I had only initially considered it because the cylinder barrels were ready made, and it would have saved me some work. But now that I think about it, they're expensive, more of a hassle, and make less power. I'll just make my own cylinders thank you very much.
Finally, when you say "For a one-off engine, make the crankcase separate from the water-cooled cylinder blocks, like many motorcycle engines, and the V8 derivatives of them " What's the reason for that? I think I know why, to avoid water potential water leaks into the crankcase, but I'm not sure...
One more thing, what do you think of the scotch yoke arrangement Engineguy? I would also like to discuss oiling and water-cooling issues...
P.S. Engineguy , I would really really appreciate it if you were to PM me with your email and/or MSN/AOL IM contact info, as I feel you're one of the people who can help me out the most...
#35
Posted 07 December 2003 - 19:19
Quote
Originally posted by Earthling
I disagree. You're not usually limited by oil sump depth, but by clutch diameter and consequently bellhousing diameter. Now, the smallest commercially availible clutch that I know of is a multi-plate 5.5" unit, which would place the bellhousing diameter at around 6", which would mean that the crank would have to be 3" above the engine's lowest point .
Not correct, there are 115 mm (4,5") clutches availible from example AP, both sintered and carbon/carbon. A 115 mm clutch wouldn't be the problem unless you use a very short stroke.
#36
Posted 07 December 2003 - 20:11
Another thing I'm somewhat concerned about right now is the matter of balance. The way I see it, I've got the equivalent of an odd-fire V6, except with a 180 degree angle between the banks, which should make things even worse I think. Another way to look at it is I've got the equivalent of a 108 degree V-10. Will this just cause me a bit of vibration at idle? That I can live with, since this going to be installed in a sports car, but the last thing I want is the damn thing tearing itself apart at 7500rpms! Would I absolutely HAVE to install a (single) balance shaft to rectify the problem? Now if only marion5sdn could chime in...
#37
Posted 07 December 2003 - 20:50
Didn't the almighty, legendary and late John Britten build his V-twins at the back yard of his house? I saw a doc with him taking out the block castings from a barrel that was in smokes and the won an AMA race. I think he also used excisting cosworth parts into hi engine, very clever.
LONG LIVE JOHN BRITTEN.....can't imagine if he built a car, must have looked as good as it goes.

#38
Posted 07 December 2003 - 21:03
Quote
Originally posted by Powersteer
After listening to a download of a BRM V16 race car i want to build an engine like it. I want to build it from billet but with all the grinding man hours it might cost a few lives.
Didn't the almighty, legendary and late John Britten build his V-twins at the back yard of his house? I saw a doc with him taking out the block castings from a barrel that was in smokes and the won an AMA race. I think he also used excisting cosworth parts into hi engine, very clever.
LONG LIVE JOHN BRITTEN.....can't imagine if he built a car, must have looked as good as it goes.![]()
Unfortunately he didn't.

Britten started out by trying to improve Ducatti engines, I believe, before moving on to his V1000 V-twins. He did start out making the stiff in his garage, but ended up in his own small factory.
Earthling, if you make your scotch yoke engine an 8, and have a flat plane crank with the middle 2 up, and the outer 2 down, most of the vibrations should cancel out.
I don't think it quite works as nicely for a 6.
#39
Posted 08 December 2003 - 09:39
Quote
Originally posted by Earthling
I guess I shouldn't have made a blanket statement like that. Allow me to rephrase; a 5.5" clutch is the smallest size I can get without selling a kidney or something. When you've budgeted ~6k for parts and materials, $2-3k is an aweful lot for just a clutch...
Another thing I'm somewhat concerned about right now is the matter of balance. The way I see it, I've got the equivalent of an odd-fire V6, except with a 180 degree angle between the banks, which should make things even worse I think. Another way to look at it is I've got the equivalent of a 108 degree V-10. Will this just cause me a bit of vibration at idle? That I can live with, since this going to be installed in a sports car, but the last thing I want is the damn thing tearing itself apart at 7500rpms! Would I absolutely HAVE to install a (single) balance shaft to rectify the problem? Now if only marion5sdn could chime in...
can you not just do a dynamic anlysis of it to determine if there is gonna be any imbalance? determine the primaries and secondaries?
Advertisement
#40
Posted 10 December 2003 - 09:54
Quote
Originally posted by Earthling
I disagree. You're not usually limited by oil sump depth, but by clutch diameter and consequently bellhousing diameter. Now, the smallest commercially availible clutch that I know of is a multi-plate 5.5" unit, which would place the bellhousing diameter at around 6", which would mean that the crank would have to be 3" above the engine's lowest point . Assuming a block "thickness" of 4.8", then this gives us 0.6" of leeway. Now assuming a header tubing diameter of 2" and an r/d of 1, we get an exhaust "height" of 2", which means that the crank centerline would have to be raised 1.4" above minimum ground clearance, which really isn't that much. You could reduce that to 1" or so by using ovalled header tubing, at least for the first few inches. (headers double up above the heads and above the engine) So your center of gravity ends up below that had you used a 120 degree V6. Remember, the heads, which are some of the most massive components would be higher up due to bellhousing clearance.
I would have to disagree with your assumption.
As you are talking about using heads from a water cooled engine (LS1 or the V6 Chevy/Buick) I would doubt that the 'block "thickness" ' would be 4.8".
You are talking about using pistons of 106.3mm diameter, which equates to 4.185". With the 4.8" block thickness gives a wall thickness of 0.3075" - 7.81mm! I would think that is a bit onn the light side, especially if you want to put cooling passages in there!
I would think that the distance from the centre of the combustion chamber to the exhaust mounting flange would be greater than 3", and therefore the mounting position of the exhausts would be lower than the bottom of the crank case.
Also, what you are proposing with the exhaust pipes seems a little impractical to me....
#41
Posted 10 December 2003 - 15:08
If youy want a big, lightweight low cg engine, why not adapt a Lycoming or Continental aero engine from a light plane or helicopter. Come to think of it, why not an ex helo turbine and gearbox.
Pat D'Rat
#42
Posted 10 December 2003 - 19:07

#43
Posted 11 December 2003 - 14:29
http://www.memagazin.../input_out.html
Perhaps you should abandon the conventional crank and use one of these arrangements......
#44
Posted 14 March 2004 - 19:15
#45
Posted 26 September 2005 - 06:42
don't let the derision of others quench your passion for your project but do listen, look and learn. You will learn from your mistakes. If you are patient and persistent building an engine from scratch is not beyond someone with your apparent technical skills and access to resources. Scoping your project with detailed time and cost estimates is a start. There's no point in running out of steam half way through. The more research you put into the fundamentals of what you are trying to achieve the less likely you will be disappointed. As some measure I would expect that your design and preparation will take 70% towards your goal. You must resist bolting into it if you find you are getting bored with the drawing board.
Technology these days (CAD-CAM/Sterelithography/CNC) allows for rapid prototyping however the time spent on the computer can equal of exceed the implementation.
After hearing what you want to do, and I'm not in a postion to cast judgments about the technical correctness, I don't think that my project which is to MAKE a twin cam head for a small engine sounds so outlandish BUT I am still scoping out the project.
Don't let your detractors stop you. For the doubters out there check out what patience, skill and determination can result in....

More information can be found at...
http://www.craftsman...m/Tomlinson.htm
BTW where are you located?
Cheers
David
#46
Posted 02 October 2005 - 03:49
I'm interested in your comments about optimal undercar aerodynimics- seems like a flat engine would be the absolute worst choice.
If you are set on a flat 6, then it would be far cheaper just to buy a watercooled Porsche engine. They come at 325HP in a road car, so imagine 400hp may be available rather easily (perhaps without opening the engine) and you'd have a proven engine that will last virtually forever.
If you want small, light and cheap, pick up Honda 4cylinder and add a turbo (although I'd sacrifice some weight and go with a VAG 1.8T)- 400HP on pump gas is very doable, with a pretty broad power band. Or, 4 cylinder subbie- surely the standard 2.5L (non-sti) ones must be very cheap in the boneyards. It will make 400 hp easily, and with far far broader powerband than you N/A 6.