
new piston ring design
#101
Posted 28 April 2011 - 08:39
would be, the inability to vary the port timing and the difficulty of keeping oil burning down along with ring and piston wear?
A four stroke would address these issues at the expense of a power stroke and a reduction in scavenge efficiency.
I have always thought opposed piston engines were the way forward for reciprocating ic engines, ever since I looked at the Deltic diesels in the 1960s.
I do not see the point in making one four stroke however.
To my thinking this counters many of the benefits and the simplicity of the basic concept.
In a way we are again at a historic point that matches the transition from reciprocating aero engines to turbojets in the late 1940s.
Hybrid cars are going to take a bigger and bigger market share (as we move towards full electric) and in a hybrid with range extender the logical ic engine will again be a constant rpm turbine.
I wonder if there will be a long enough shelf life for the PatOp to allow it to succeed in the market place?
Advertisement
#102
Posted 28 April 2011 - 11:04
24gerrard, on Apr 28 2011, 16:39, said:
A four stroke would address these issues at the expense of a power stroke and a reduction in scavenge efficiency.
Hybrid cars are going to take a bigger and bigger market share
Thats not a valid argument, 2 strokes do not have complete power strokes and a 4 stroke eats a 2 stroke alive for scavenge efficiency.
Not because they are better but because people brains are being pumped full of crap on the subject. But I must admit the new "Hybrid" S400 Benz I spent a few hours in the back seat of on Teusday was nice when it turned off when stopped at red lights.
24gerrard, on Apr 28 2011, 16:39, said:
Would I be correct in saying that the main things against the two stroke PatOp engine
would be, the inability to vary the port timing and the difficulty of keeping oil burning down along with ring and piston wear?
2 strokes have had simple standard variable port timing since the 70's and yes oil around the ports is the issue - more oil means pollution, no oil means seizure/short life or expensive alternates.
I also note that Man's and OPOC's engines are, IMO, far from optimised in their port layouts and are equivalent of the very first 2 strokes, one hundred years later this is pretty dissapointing.
#103
Posted 28 April 2011 - 13:01
cheapracer, on Apr 28 2011, 05:04, said:
Exactly WHICH method of scavenging are you referring to when you say "2 strokes do not have complete power strokes and a 4 stroke eats a 2 stroke alive for scavenge efficiency". Not uniflow scavenging, as it is MORE effective at that than a 4-stroke is as far as I know. Of course, if anyone has data that can refute that claim, I am always happy to learn...Thats not a valid argument, 2 strokes do not have complete power strokes and a 4 stroke eats a 2 stroke alive for scavenge efficiency.
Not because they are better but because people brains are being pumped full of crap on the subject. But I must admit the new "Hybrid" S400 Benz I spent a few hours in the back seat of on Teusday was nice when it turned off when stopped at red lights.
2 strokes have had simple standard variable port timing since the 70's and yes oil around the ports is the issue - more oil means pollution, no oil means seizure/short life or expensive alternates.
I also note that Man's and OPOC's engines are, IMO, far from optimised in their port layouts and are equivalent of the very first 2 strokes, one hundred years later this is pretty dissapointing.
Edited by unclematt, 28 April 2011 - 22:37.
#104
Posted 28 April 2011 - 19:16
However it still has serious weaknesses to solve.
The Mazda RX-8 / 231 bhp is quite cheap-to-buy here, because its capacity is measured the wrong way: instead of 2600cc, it is taken as 1300cc.
The happy new owner soon discovers that his nice looking car is a thirsty special purpose toy.
In the official combined cycle it emits 299 gr CO2 / Km; that "clean".
In comparison, the small Fiat TwinAir 85bhp, in the same combined cycle emits 95 gr CO2 / Km.
I know they are not comparable. Yet it gives an idea.
I remember the S2000 of Honda, with 240 bhp.
It was also “clean”, with the catalyst working overtime.
Additional air was supplied to the exhaust manifold of the S2000 to burn the unburned fuel!
Unless I am wrong, the RX-8 idling consumption is 1.2 lit/hour (some 40% better than the previous rotary RX-7).
At Idle valves the pattakon VVA roller Civic prototype idles at 330 rpm, stoichiometric, with 1 lit of fuel per three hours, with flat torque curve and peak power at 9000 rpm.
The truth is that after so many years of evolution, the Wankel Rotary is still not ready for normal applications.
By the way, do you know that the OPRE single cylinder power unit for small airplanes, parapente etc, shown at Flyer is way more vibration free than the Wankel Rotary?
The OPRE with two counter-rotating propellers secured on its crankshafts, leaves its basis (the chassis of a small airplane, for instance) perfectly rid of inertia vibrations and perfectly rid of power pulses vibrations.
The Wankel rotary cannot: its basis cannot be rid of the power pulses vibrations.
Besides, at flight it is the total weight of take-off that counts: the engine plus the fuel.
If PatOP, OPRE, OPOC prove only “a-little-better” than the state-of-the-art 4-stroke, they are dead.
Nobody cares about “a-little-better”; they must work “a-lot-better” and be a lot more fuel-efficient.
The opposed pistons enable the uniflow through scavenging.
The crosshead pistons are used for scavenge pumps at the other side.
A spool in the exhaust pipe (like Honda’s spool, or Yamaha’s exup) is more than adequate for any asymmetry, especially when a volumetric piston-type scavenging pump is used; it is also continuously variable.
It is a full engine with only a crankshaft, two pistons, 4 conrods, and an unloaded simple casing (and a couple of reed valves into the pump).
The friction losses are less than half of the 4-stroke, the power close to double, the power-to-weight ratio way than double and the cost to make lesser than half.
For the lubrication issue:
Because the pistons do not touch the liners (they have a better than 4-cycle lubrication at the sliders) they don’t need to see any oil drop.
The oil that cools the pistons, as they get out the liner and stay naked into the casing, clings on the skirts, and little of it remain on the skirt as it get past the oil seal at the ends of the liner. This quantity of oil has no reason to reach the ports before reaching the rings.
Navistar makes 4-stroke diesels; any kind of them: I-4, I-6, V8 etc.
But they are complicated, heavy, expensive and not as fuel efficient as the OPOC can be.
They know that any additional part of the engine, beyond the three main components (piston, rod, crankshaft) adds weight, friction and troubles.
The guess is that Bill Gates nodded only when OPOC promised better mileage.
Wankel is a nice toy that can, at its best, turn 25% of the fuel into mechanical energy. OPOC is intended for nearly 50%.
Thanks
Manolis Pattakos
#105
Posted 29 April 2011 - 03:38
As for the efficiency claims, the best I've seen published for this engine were 42% BTE. A modern class 8 truck 4-stroke diesel can easily get 45% BTE while meeting emissions standards, and is good for a million miles.
The only valid claim that Ecomotor makes is regarding their engine's power-to-weight. However, it gets a high power-to-weight with high BMEP rates and high rpm. This approach will lead to short engine life and high SFC. It will also lead to a rough running and noisy engine, which will be unacceptable for the commercial market.
The OPOC engine has the same limitations as previous opposed piston designs: The combustion efficiency is poor due to the injector location in the cylinder wall, and the piston crown/ring pack thermal loads are high due to high BMEP rates and 2-cycle operation. Unless they solve these fundamental issues, their OPOC engine will be no more commercially successful than its predecessors.
slider
#106
Posted 29 April 2011 - 06:45
bigleagueslider, on Apr 29 2011, 13:38, said:
42% is very good for a small diesel. Diesel efficiency improves with cylinder size. Having said that - IMO the PatOP and the PatOPOC are better designs than OPOC.As for the efficiency claims, the best I've seen published for this engine were 42% BTE. A modern class 8 truck 4-stroke diesel can easily get 45% BTE while meeting emissions standards, and is good for a million miles.
#107
Posted 29 April 2011 - 14:36
Here are the pistons of the PatOP prototype
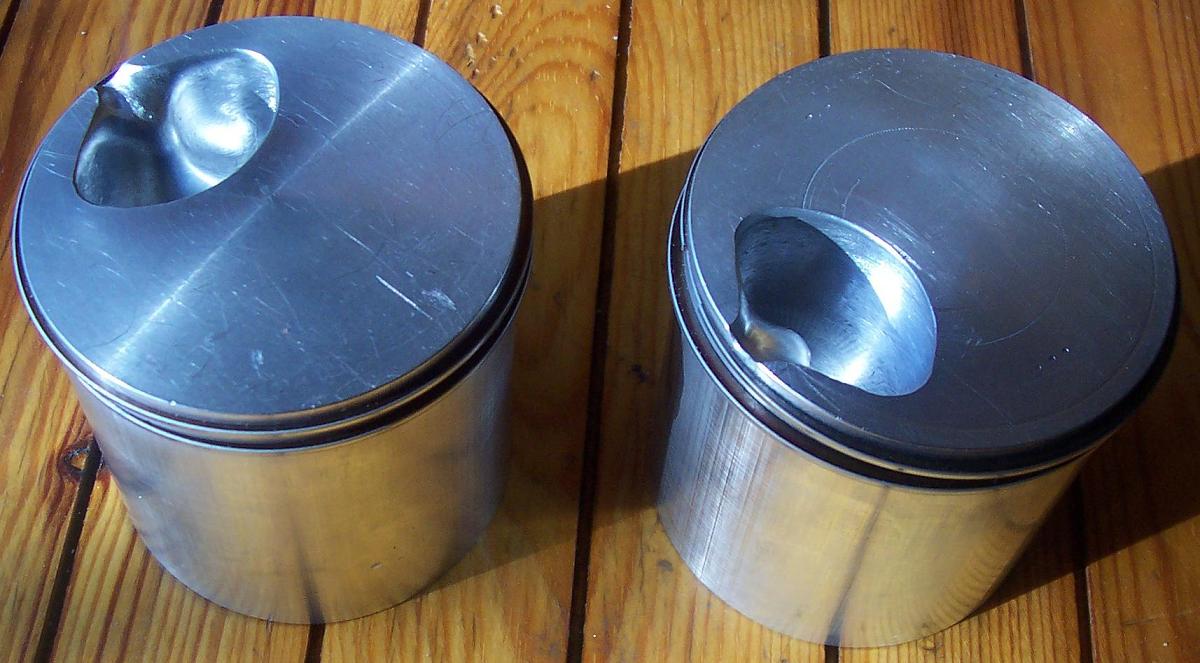
The engine has never had any glow-plug, but it cool-starts without a second try.
It seems that such a bowl provides better aerodynamics and thermodynamics than a conventional four-stroke bowl.
In a four-stroke the valves make the chamber non-uniform, thermally at least: red-hot exhaust valves, cool intake and cooler aluminum to help NOx HC, CO formation.
The valve pockets on the piston spoils the motion of the compressed air towards the bawl.
As the two flat / smooth piston crowns “touch” each other at the CDC (Combustion Dead Center), all the air is squeezed into the bowls and stay there until it get burned (because the pistons keep on “touching” for 35% longer than in the conventional).
Practically, the surface-to-volume ratio during combustion (where the highest coefficient of heat-transfer) is only the bawls (the flat areas are almost isolated, i.e. they see no burning-gases).
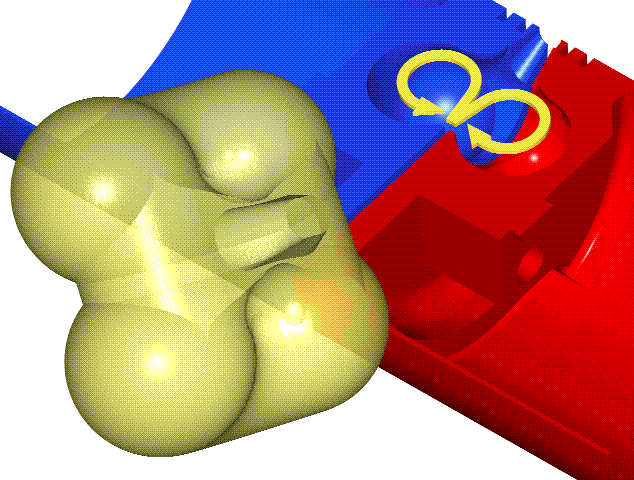
The strong squeeze generates a swirling-vortex into each bowl capable to accelerate the combustion.
The geometrical symmetry and the thermal smoothness eliminate the hot-spots that generate NOx, the cooler for HC, the unevenness for soot etc.
Then it comes the highly efficient uniflow (through) scavenging to optimize breathing.
Then it comes the lower friction of the two stroke.
Don’t count the number of the connecting rods; they are arranged “parallel”, sharing the load.
Think if there is a significant difference between a centrally located heavier / wider connecting rod carrying the complete load, and a pair of “parallel” connecting rods, each carrying the half load.
The friction heavily depends on the mean piston speed.
The PatOP prototype has a total stroke of 64+64=128mm (total height of the engine: 500mm), which is extreme for conventional engines having 635cc cylinder capacity. However, at 4000 rpm (wherein the power of the current high-speed conventional Diesels drops steeply) the mean piston speed of the PatOP is only 8.5 m/sec.
Then it comes the full balance of the inertia forces and moments.
With two opposed pistons and one cylinder, the PatOP is more vibration free than the conventional four in line (even those using two counter-rotating 2nd order balance shafts).
Then it comes the simplicity.
The (combustion) liner is loaded symmetrically (no thrust loads, no bending / deformation, no temperature differences around the cylinder axis); it is so unloaded that you can move it easily to make asymmetrical the timing (yet this is not worthy when a volumetric scavenging pump is used).
The piston is symmetrical: it doesn’t need an oval shape as the conventional pistons.
The crosshead – at the opposite side of the combustion – is cold and is used as a built-in low-cost small dead-volume scavenging pump. An external turbo charger is optional.
The casing of a highly supercharged direct injection Diesel needs not be strong, nor heavy.
The loads are taken internally, leaving only the torque pulses to the casing.
It needs not even a head gasket.
The previous cannot justify a 50% better fuel efficiency over the current direct injection Diesels (as EcoMotors "stupidly" claims).
However, a 5% improvement (which is still a great step ahead) seems possible.
Thanks
Manolis Pattakos
#108
Posted 30 April 2011 - 00:18
bigleagueslider, on Apr 28 2011, 21:38, said:
I don't see your concerns reflected in development in the field with regard to opposed piston engines. Here is an opposed piston engine company that utilizes a 4-stroke. They don't seem to be hampered by the issues you mention with side mounted injectors.The OPOC engine has the same limitations as previous opposed piston designs: The combustion efficiency is poor due to the injector location in the cylinder wall, and the piston crown/ring pack thermal loads are high due to high BMEP rates and 2-cycle operation. Unless they solve these fundamental issues, their OPOC engine will be no more commercially successful than its predecessors.
slider
http://pinnacle-engines.com/index.html
http://www.greencarc...e-20110331.html
Also, I read somewhee that OPOC uses oil jets to cool their piston crown/ring pack, so the thermal loads you mention perhaps aren't an issue for them. I will see if I can find that source and post it.
Edited by unclematt, 30 April 2011 - 01:33.
#109
Posted 30 April 2011 - 08:58
unclematt, on Apr 30 2011, 01:18, said:
I don't see your concerns reflected in development in the field with regard to opposed piston engines. Here is an opposed piston engine company that utilizes a 4-stroke. They don't seem to be hampered by the issues you mention with side mounted injectors.
http://pinnacle-engines.com/index.html
http://www.greencarc...e-20110331.html
Also, I read somewhee that OPOC uses oil jets to cool their piston crown/ring pack, so the thermal loads you mention perhaps aren't an issue for them. I will see if I can find that source and post it.
This one looks like a way to get around patents.
Why two cranks and why in four stroke form does it still have rings going over port openings?
IMO not a good way to use sleeve valves.
#110
Posted 01 May 2011 - 01:13
unclematt, on Apr 29 2011, 17:18, said:
I don't see your concerns reflected in development in the field with regard to opposed piston engines. Here is an opposed piston engine company that utilizes a 4-stroke. They don't seem to be hampered by the issues you mention with side mounted injectors.
I was an engineer on a DOD sponsored high pressure OP diesel 2-stroke program several years ago. Here's a technical paper on the CFD analysis work done on the injector by Los Alamos National Labs. It covers some of the basic issues with injector location, spray penetration and mixing.
http://www.osti.gov/...able/206549.pdf
Regards,
slider
#111
Posted 01 May 2011 - 01:47
bigleagueslider, on Apr 30 2011, 19:13, said:
Thanks Big league! I will read it tonight and get back to you.I was an engineer on a DOD sponsored high pressure OP diesel 2-stroke program several years ago. Here's a technical paper on the CFD analysis work done on the injector by Los Alamos National Labs. It covers some of the basic issues with injector location, spray penetration and mixing.
http://www.osti.gov/...able/206549.pdf
Regards,
slider
#112
Posted 01 May 2011 - 06:00
The penetration and mixing is a pure physical process.
The spray leaving the injector nose doesn’t know whether the engine operates at 1000 rpm or at 5000 rpm. The only that the spray feels is the hot, moving, compressed air.
The struggle in the Diesel engine is to realize the penetration and mixing of the fuel in the most efficient way. And the limiting factor (the enemy) is the time.
In the advantages of the OPRE, PatOP and PatFour, add one more significant: the additional time the piston dwells near the CDC (combustion dead center).
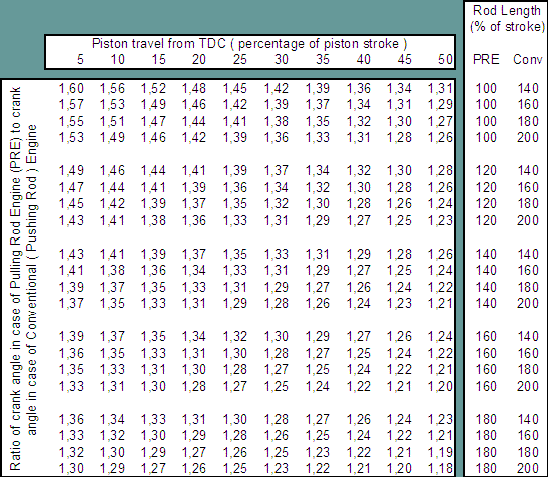
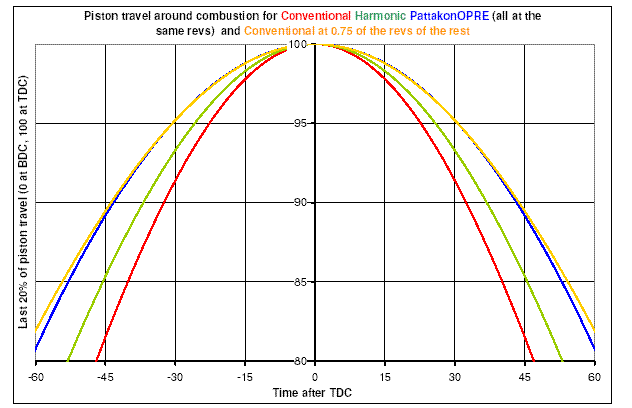
Fuel's Viewpoint :
The following animation shows the piston motion near the TDC of the OPRE engine revving at 6000 rpm versus the Conventional revving at 4500 rpm, for equal piston stroke and equal (1.65) con-rod to stroke ratio.
Without seeing the kinematic mechanism, how can you reply to: " WHICH is the Conventional and WHICH is the OPRE ? "
Suppose you are a fuel droplet injected either into the cylinder of the conventional or into the cylinder of the OPRE.
What you 'see' is the 'walls' of the combustion chamber, i.e. the cylinder head (if any), the piston top and the cylinder wall.
What you 'touch' is air of some temperature, pressure, turbulence and swirl.
As you have no way to 'see' (or 'feel') the crankshaft or the kinematic mechanism, you cannot say (for sure) that you were injected and burned into the OPRE revving at 6000 rpm or into the Conventional revving at 4500 rpm.
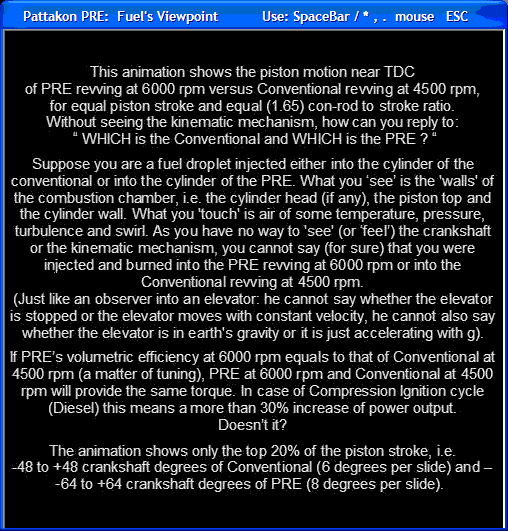
Combined with the half piston speed of the opposed piston arrangement and the highly efficient uniflow scavenging, the additional time for the injection / combustion of the fuel, enables far higher power density. At the lower revs this extra time improves the fuel efficiency and the clean exhaust
By the way, with the bowl on the piston crowns of the PatOP (my previous post), what are the desadvantages as compared to the conventional state-of-the-art direct injection Diesels?
Thanks
Manolis Pattakos
#113
Posted 01 May 2011 - 08:37
One disadvantage might be uneven temperature across the piston crown - higher temperatures on the "bowl" side. (Considering thermal expansion of the piston - not combustion chamber thermal smoothness which must be excellent)
On the "plus" side"
The fuel is injected along an axis of symmetry and this remains an axis of symmetry as the pistons move apart.
The squish geometry lends itself to creation of ideal air motion, with high velocity in the opposite direction to the fuel spray. Congratulations on your combustion chamber design. Did the shape evolve much with CFD or is this similar to your starting design?
I must say, the more I look at this engine the more I like it.
#114
Posted 01 May 2011 - 11:19
After the war much of the technology was used in such engines as the English Electric Deltic and of course the Commer TS3 and 4 from which the opposed piston design reached a practical (at the time) production vehicle level.
I agree with gruntguru that this engine looks better the more it is investigated.
I like the way that piston side load is transfered to the slider allowing the rings to work better and the resultant geometry that allows the pistons to dwell longer at TDC and BDC.
I see this thread headed 'new piston ring design' as an attempt to cure the remaining problems.
It would be nice to replace the long skirt pistons with nice light slipper pistons thanks to the lack of side loads, unfortunately the skirts remain necessary to achieve an acceptable level of ring lubrication.
This problem will not be cured until a better method than allowing the top rings to transit over the open exhaust and inlet ports is found.
I think this can be achieved without compromising the design by going four stroke or having to accept high oil burning (relative) and piston/ring wear.
My main misgiving is whether the needed and justified development can be undertaken before hybrids become widespread using a turbine generator as a range extender. This is the same issue that killed piston aero development in the late 1940s when the turbojet took over.
#115
Posted 01 May 2011 - 13:25
24gerrard, on May 1 2011, 05:19, said:
Although there is a new gas turbine design ( http://gogreenmagazi...iency-increase/ ) that promises better efficiency, unless compression ratios are increased in their design, I doubt gas turbines will ever be efficient enough to serve in a hybrid.My main misgiving is whether the needed and justified development can be undertaken before hybrids become widespread using a turbine generator as a range extender. This is the same issue that killed piston aero development in the late 1940s when the turbojet took over.
And I continue to point out that both manolis AND OPOC claim to have a "scraper ring" that allows lubrication past liner ports without effecting emmissions. Until that is proven one way or the other with finality, I will continue to wonder if their solutions are not workable...
#116
Posted 01 May 2011 - 13:27
gruntguru, on May 1 2011, 02:37, said:
Though I lack supporting evidence, I am pretty sure your concerns are well founded. Lets hope we are both wrong. :-)Just my impressions:
One disadvantage might be uneven temperature across the piston crown - higher temperatures on the "bowl" side. (Considering thermal expansion of the piston - not combustion chamber thermal smoothness which must be excellent)
#117
Posted 01 May 2011 - 13:31
Edited by unclematt, 01 May 2011 - 13:50.
#118
Posted 01 May 2011 - 13:35
bigleagueslider, on Apr 30 2011, 19:13, said:
I read the paper you posted, and I am not seeing anything in it that shows side mounted injectors are problematic. Were there specific passages in the paper you could post to further illustrate your concerns?I was an engineer on a DOD sponsored high pressure OP diesel 2-stroke program several years ago. Here's a technical paper on the CFD analysis work done on the injector by Los Alamos National Labs. It covers some of the basic issues with injector location, spray penetration and mixing.
http://www.osti.gov/...able/206549.pdf
Regards,
slider
#119
Posted 01 May 2011 - 17:15
The bowl design is simpler than it seems.
Take an angular part, about 150 degrees, of the typical bowl of the current four stroke direct injection Diesel (like a piece of a pie), and put its “symmetry” axis as close to the injector as possible, leaving a safety distance from the piston ring-lands.
Do the same on the opposite piston, and you have a quite compact bowl (big volume to surface ratio), near to the injector nose.
With one injector per cylinder:
in the case of flat crowns (i.e. without bowls), the spray has to travel some 80mm (i.e. the cylinder bore) to find all the air,
in the case of piston crowns having bowls (PatOP prototype), the spray needs to travel less than 30mm (one third). And the air, during the injection, comes from the opposite direction (upstream) relative to the fuel spray, significantly improving its vaporization and mixing.
For true high-speed direct injection Diesels (peak power at 6000+ rpm) this is vital.
Think: at 6000 rpm, in 1 millisecond (i.e. in the time necessary for the spray to penetrate for some 50mm into the compressed air) the crankshaft rotates for 36 degrees.
24gerrard wrote: “I like the way that piston side load is transfered to the slider allowing the rings to work better and the resultant geometry that allows the pistons to dwell longer at TDC and BDC.”
No, the longer piston dwell is only at the TDC (or better at the CDC or Combustion Dead Center).
At the BDC the piston dwell is shorter than in the conventional engine.
The volumetric scavenging pump, at the other side of the piston, stays longer at its maximum volume, improving the breathing.
The bak side of the piston crown (which has not a piston pin, nor piston pin bosses, nor the small end of a connecting rod) is free for the oil to cool it, where it needs a further cooling.
The deformation, if any, of the piston crown is not critical, unless it affects the ring-lands.
Here is another advantage:
The four stroke needs a good safety clearance between the cylinder head and the pistons: at high revs, during the overlap TDC (no pressure onto the piston crown), the tension of the connecting rod is dangerous for the integrity of the engine.
The two stroke, on the other hand, has always high pressure above the piston crowns at the CDC, enabling way smaller clearance between the two opposed pistons (i.e. the out of the bowl air, at the CDC, can reach the minimum possible).
Unclematt wrote: “Hey Manolis, I think the arrows representing injector flow in your combustion chamber illustration are pointed in the opposite direction of where they should point. You have the injector flow coming from the squish area and not the hole in the piston combustion chamber...”
No.
The arrows depict the air stream coming from the flat areas as they squish the in-between the pistons air to force it into the bowl. The fuel injector is at the opposite side to inject upstream (oppositely to the air stream).
In the photo:
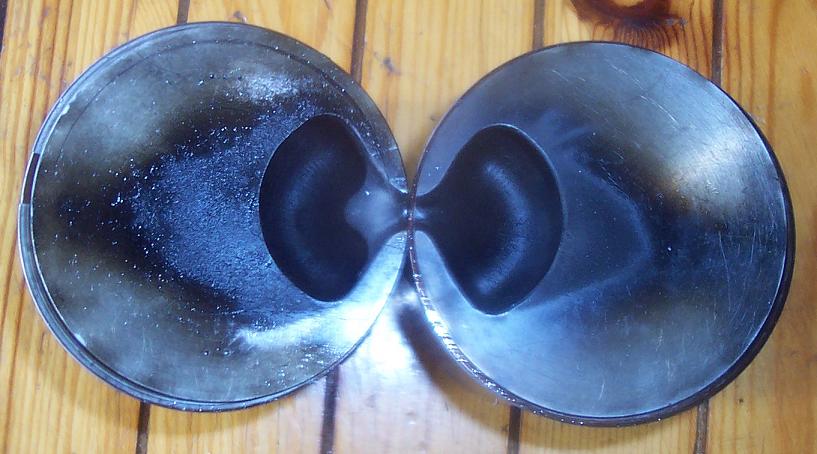
the crowns outside the bowls are clean: the squished air sweeps the fuel droplets back to the bowl.
The injection system of the prototype is anything but optimized.
In the Sulzer RTA engines, i.e. the most efficient engines with over 50% brake thermal efficiency running on residual fuel (5% sulfur), the main care is to keep the fuel from hitting the metal surfaces.
The purpose here is similar: to use the air motion to “spit” the fuel back into the bowl and burn it with the least touching with the walls.
Thanks
Manolis Pattakos
Advertisement
#120
Posted 01 May 2011 - 17:53
What is the roughed up area on the left piston to the left of the combustion chamber? And how about the thermal differences caused across the piston crown by the asymmetrical combustion chamber? Any concerns there?
Edited by unclematt, 01 May 2011 - 17:56.
#121
Posted 01 May 2011 - 21:01
#122
Posted 02 May 2011 - 11:10
24gerrard, on May 1 2011, 21:19, said:
I don't think the skirts bear on the bore so the long skirt design has no disadvantage in this case.It would be nice to replace the long skirt pistons with nice light slipper pistons thanks to the lack of side loads, unfortunately the skirts remain necessary to achieve an acceptable level of ring lubrication.
24gerrard, on May 1 2011, 21:19, said:
GT has a lot of advantages but fuel efficiency is a long way short of Diesel (especially at the micro-turbine scale)My main misgiving is whether the needed and justified development can be undertaken before hybrids become widespread using a turbine generator as a range extender. This is the same issue that killed piston aero development in the late 1940s when the turbojet took over.
#123
Posted 02 May 2011 - 11:58
unclematt, on Apr 28 2011, 21:01, said:
Exactly WHICH method of scavenging are you referring to when you say "2 strokes do not have complete power strokes and a 4 stroke eats a 2 stroke alive for scavenge efficiency". Not uniflow scavenging, as it is MORE effective at that than a 4-stroke is as far as I know. Of course, if anyone has data that can refute that claim, I am always happy to learn...
You are talking about scavenging in terms of sheer volume (lets not forget you are comparing an engine, ie; the 2 stroke, that is always supercharged otherwise it won't even run against one that is not) and I am talking about scavenging in terms of efficiency such as ability to keep intake and exhaust gases separate and controlling/retaining appropriate volumes within the cylinder at all speeds.
I also don't believe "Uniflow" is as effective as it could be in the OPOC or PatOP as I have been into 2 stroke exhausts for a loooong time and I consider that the circular perimeter porting that they both have not only is about 50% effective because of wave reflection and maybe inconsistently upsetting the pre charge over the speed range. Moving exhaust gases is not just about having bigger holes.
Edited by cheapracer, 02 May 2011 - 12:12.
#124
Posted 02 May 2011 - 16:51
The reflection of the flash of the camera makes the surface seem rough at the intake piston at left.
What the thermal differences across the piston can cause to a piston like this?
If you mean the deformation, the crosshead design is insensitive to this.
As for the ring lands, they can deform axially without a problem.
Besides, the cooling of the back side of the piston crown is way easier than in the conventional pistons with the piston pin, the piston pin bosses and the small end of the connecting rod hiding the back side of the piston crown from the crankcase oil.
Many conventional pistons – which are way more sensitive to deformation – have the bowl offset from the cylinder axis (direct injection Ford engines, for instance).
Thanks
Manolis Pattakos
#125
Posted 02 May 2011 - 17:41
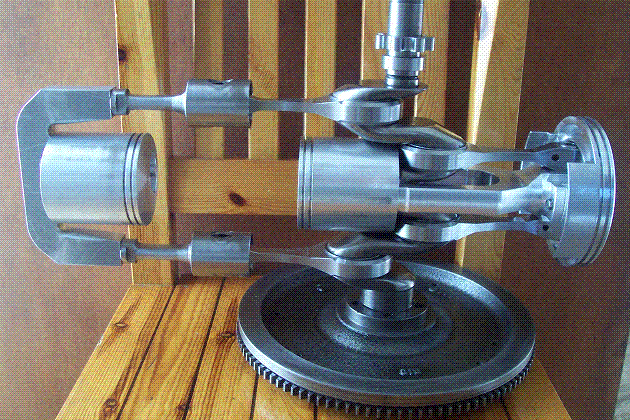
Spot on the big diameter piston at the right.
Here:
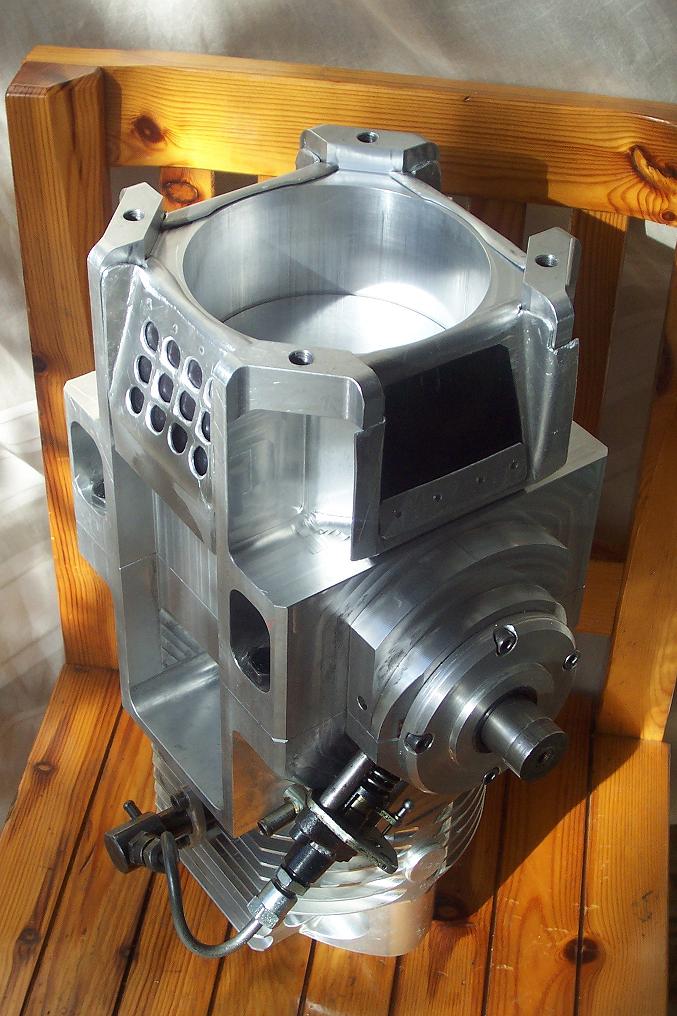
you can see the top end of the big diameter piston inside the scavenging pump of the PatOP prototype engine.
Its diameter (bore) is 130mm, its stroke is 64mm (equal to the stroke of each opposed piston).
The big piston is slidably fitted into the scavenging pump cylinder.
Its piston skirt takes the thrust loads of the intake-combustion-piston, leaving the combustion liner rid of thrust loads.
The scavenging pump capacity is 850cc, giving a geometrical scavenging ratio of 850/635=1.34
At front-right you see the one inlet-reed-valve (there is one more, diagonally).
At front-left you see the one exit (transfer) reed-valve (there is one more, diagonally).
Here you can see the same reed valves from another view point:
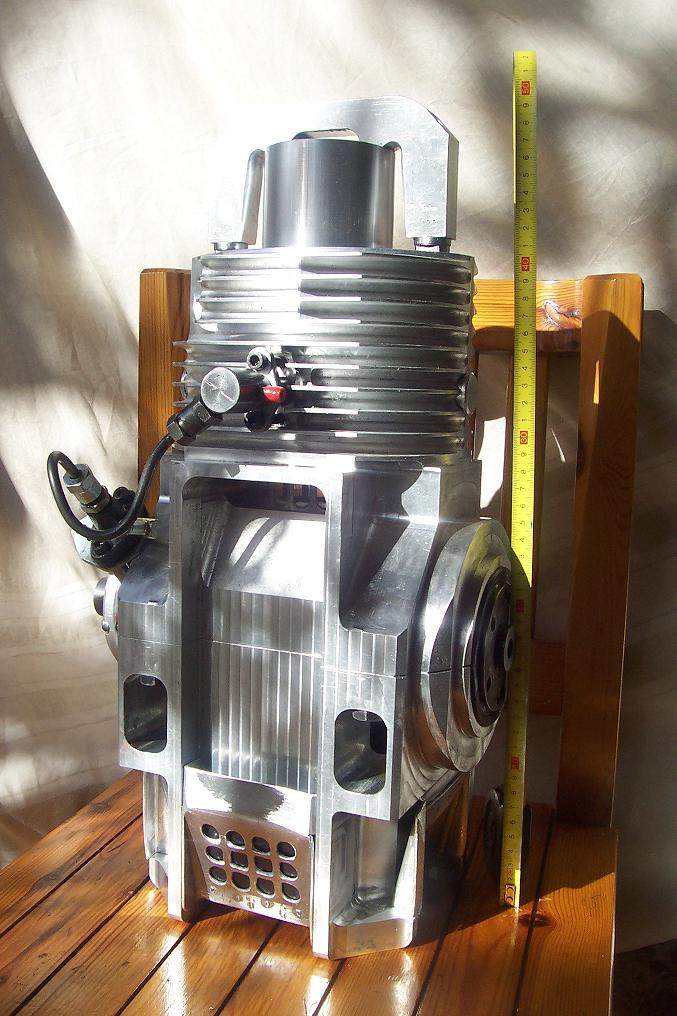
Spot on the “triangular” opening at the side (backside) of the intake-reed-valve.
There are two such “triangular” openings at the sides of each intake reed valve.
Here is where the PatOP engine finds fresh / clean air.
Operation:
As the two opposed pistons approach each other, the big diameter piston creates a vacuum into the scavenging cylinder.
Through the “triangular” openings and the intake-reed-valves, fresh air is suctioned (the exit-reed-valves stay closed) into the scavenging pump cylinder.
The long dwell of the pistons at the CDC (i.e. the long dwell of the big piston at the maximum volume of the scavenging pump) improves the volumetric efficiency of the scavenging pump.
The process is identical to the suction cycle of the four stroke engine.
Instead of the conventional intake poppet valves, the reed-valves make the control of the air.
After the CDC (combustion dead center) the big piston moves downwards, compressing the air inside the scavenging pump cylinder.
The intake reed valves close.
When the pressure inside the scavenging pump cylinder increases over the pressure into the transfer “pipe” / manifold (i.e. into the volume between the exit-reed-valve and the intake ports), the exit-reed-valves open and the piston displaces the air from the scavenging cylinder to the transfer “pipe”, wherein it stays until the intake ports open by the intake piston.
For the last part (say one quarter) of the stroke downwards, the exit-reed-valves are open, the intake ports are open, the exhaust ports are open and the last air from the scavenging cylinder is displaced to the tranfer pipe.
The process is similar to the exhaust stroke of the four stroke engine.
Instead of the conventional exhaust poppet valves, the exit-reed-valves make the control of the air.
Note here the very small dead volume of the scavenging pump. Almost as small as the dead volume of a four-stroke engine.
Note also that the air has nothing to do with the crankcase (and the oil there).
Note also the big area of the reed valves as compared to the poppet valves of a similar four stroke engine.
Note also that the bad characteristics of a short stroke engine (small volume to surface ratio, poor thermal efficiency, etc) are advantages for a short stroke scavenging pump.
So, the scavenging pump of the PatOP is a built-in volumetric piston-type pump.
No matter what the exhaust pressure is, the “volumetric” scavenging pump of the PatOP displaces 850cc of air per crank rotation towards the intake ports.
With such quantity of air entering through the intake ports per cycle,
with such long combustion cylinder (79.5mm bore, 64+64=128mm stroke),
with uniflow scavenging,
and with the exhaust ports opening first,
most of the exhaust gas will leave the combustion cylinder.
The additional air makes another significant thing: it cools internally the cylinder, the exhaust ports, the piston crowns and the piston rings.
The conventional two-stroke engine has peaky torque curve.
The PatOP engine is not based on the resonance of a tuned exhaust (Caaden), and can operate even without an exhaust manifold.
Think:
In every two rotations of the crankshaft of a 635cc four stroke engine, some 635cc of fresh air pass through the cylinder to the exhaust.
In every two rotations of the crankshaft of the 635cc PatOP prototype engine, some 1700cc of fresh air pass through the combustion cylinder to the exhaust.
Then think that, with the additional time for its combustion, the two stroke PatOP direct injection Diesel can keep its torque at 35 to 40% higher revs than the conventional four stroke direct injection Diesel.
Think also:
In order to supercharge the PatOP, you have the option to use a conventional turbocharger.
In order to supercharge the PatOP, you can alternatively put an obstacle (like a spool valve or an "ex-up" valve) at the exhaust, to keep higher the exhaust pressure.
I hope it is clear now why the PatOP two-stroke engine has more flat torque curve and more wide rev range than the four stroke engines.
Thanks
Manolis Pattakos
#126
Posted 03 May 2011 - 04:53
manolis, on May 3 2011, 01:41, said:
Think:
In every two rotations of the crankshaft of a 635cc four stroke engine, some 635cc of fresh air pass through the cylinder to the exhaust.
In every two rotations of the crankshaft of the 635cc PatOP prototype engine, some 1700cc of fresh air pass through the combustion cylinder to the exhaust.
I don't expect these "superior 2 stoke based on a 2:1 factor" simplistic statements from you Man.
Simply - A 4 stroke opens it's intake well before TDC and closes well after BDC thats where cam timing numbers such as 40/80 (80/40) come from whereas a 2 stroke has ports open symetrically and often at the wrong time and only over a very narrow rpm band is it perfect - either side of that it's either too efficient leading to bad emissions or unefficient leading to poor power and still bad emissions.
On a supercharged 4 stroke I can stuff 1700cc of air in and do it in a controlled manner such as that I can capture near 100% of it in the cylinder over a wide RPM band, you can not do that with a 2 stroke.
manolis, on May 3 2011, 01:41, said:
I hope it is clear now why the PatOP two-stroke engine has more flat torque curve and more wide rev range than the four stroke engines.
What is clear is you are comparing a supercharged engine against a non supercharged engine - if I however supercharge the 4 stroke as well the comparison will change somewhat.
The only advantage a 2 stroke has is superior manufacturing cost, thats why people still try to sort it out but every (car) manufacturer has long given up on them with the exception of Orbital who stirred some interest and now Lotus with a concept so complicated why bother.
#127
Posted 03 May 2011 - 05:20
cheapracer, on May 2 2011, 19:58, said:
I consider that the circular perimeter porting that they both have not only is about 50% effective because of wave reflection and maybe inconsistently upsetting the pre charge over the speed range. Moving exhaust gases is not just about having bigger holes.
I would be looking at basic loop scavenging for these engines, I feel that they would benefit from having a narrower shear point between the 2 gases that would be far easier to control (where the exhaust and intake meet and travel through the cylinder together). I think the current setup with 360 degrees of ports is offering nothing except poor flow and wave reflection that will be making the shear point of the gases very wide and inconsisstent. Of course perfection is when you can close the port with the piston at the same time as the shear point reaches there (btw, "shear point" is my own naming).
Not knowing enough about emissions things I wouldn't have a clue which side the injector would be better on as obviously the port side is going to have some dead exhaust gas lingering, I imagine it may be better to burn through them to keep temps down and the fresher charge on the opposite side will help to get a burn completely across the cylinder (?) so that would put the injector on the same side as the ports.
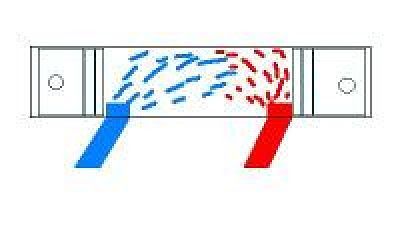
More and bigger holes is not better!
Man, I would be also looking at an adjustable volume plenum from your supercharger to the intake port, this will give you a chance to tune the intake pressure (but not the volume) to suit whatever the exhaust waves are doing.
Oh and OPOC if you're reading this you owe me a million for the advice.
Edited by cheapracer, 03 May 2011 - 05:32.
#128
Posted 03 May 2011 - 06:07
cheapracer, on May 3 2011, 14:53, said:
A major feature of opposed piston 2 strokes is asymmetrical timing capability.Simply - A 4 stroke opens it's intake well before TDC and closes well after BDC thats where cam timing numbers such as 40/80 (80/40) come from whereas a 2 stroke has ports open symetrically and often at the wrong time and only over a very narrow rpm band is it perfect - either side of that it's either too efficient leading to bad emissions or unefficient leading to poor power and still bad emissions.
cheapracer, on May 3 2011, 14:53, said:
Yes you can and the PatOP probably captures 1270cc or more.On a supercharged 4 stroke I can stuff 1700cc of air in and do it in a controlled manner such as that I can capture near 100% of it in the cylinder over a wide RPM band, you can not do that with a 2 stroke.
cheapracer, on May 3 2011, 14:53, said:
An externally scavenged 2-stroke is not necessarily supercharged. The PatOP operates at approximately 1 atm charge pressure and can still be subsantially supercharged beyond that. For equivalent thermal stress levels the PatOP will be making approximately twice the power of the 1270cc 4 stroke.What is clear is you are comparing a supercharged engine against a non supercharged engine - if I however supercharge the 4 stroke as well the comparison will change somewhat.
#129
Posted 03 May 2011 - 07:22
gruntguru, on May 3 2011, 14:07, said:
A major feature of opposed piston 2 strokes is asymmetrical timing capability.
I actually thought that an exhaust port or inlet that opened 50 degrees before BDC also closed at 50 degrees ABDC so tell me your definition of asymetrical.
gruntguru, on May 3 2011, 14:07, said:
Yes you can and the PatOP probably captures 1270cc or more.
Probably does at one narrow point of it's rev range, it's what happens for the rest of the rev range either side of that point thats the big issue.
gruntguru, on May 3 2011, 14:07, said:
An externally scavenged 2-stroke is not necessarily supercharged. The PatOP operates at approximately 1 atm charge pressure and can still be subsantially supercharged beyond that. For equivalent thermal stress levels the PatOP will be making approximately twice the power of the 1270cc 4 stroke.
Name a 2 stroke that isn't supercharged somewhere in it's system ...
You can supercharge the hell out of the PatOP and I can supercharge the hell out of a 4 stroke but only one of them is going to capture the bulk of the volume while the other one is going to blow a considerable amount straight out the exhaust ports - you could add valves to help but then whats the point of the excersize, may just as well build the 4 stroke.
Sound it out as you want but we both know in the real world that normal sized 2 strokes do not make double the power of 4 strokes nor are they quiet, clean, fuel efficient or generally likeable

#130
Posted 03 May 2011 - 10:13
Without poppet valves of course.

I notice the wear marks on the rotating component image.
This must mean very poor lubrication of the piston skirts if there is no piston side load.
(caused by reducing the oil volume available to reduce burning oil through the ports no doubt)
So there is a reason to get rid of the long skirts but no way with the current problems.
I think I know how to do it and one million is not enough cheapy.
#131
Posted 03 May 2011 - 11:33
cheapracer, on May 3 2011, 17:22, said:
Port-timed, single piston 2 strokes have inlet opening centred around BDC, likewise exhaust. The opposed piston design can have two seperate BDC's and therefore an exhaust period centred prior to "average BDC" and an inlet period centred after "average BDC".I actually thought that an exhaust port or inlet that opened 50 degrees before BDC also closed at 50 degrees ABDC so tell me your definition of asymetrical.
cheapracer, on May 3 2011, 17:22, said:
You are trapped in your experiences of conventional 2 stroke engines. The OP design can scavenge 100% + across a wide rev range.Probably does at one narrow point of it's rev range, it's what happens for the rest of the rev range either side of that point thats the big issue.
cheapracer, on May 3 2011, 17:22, said:
99% of them. You are confusing scavenging with supercharging. Many have some degree of supercharge courtesy of pipe tuning or some stagger of valve/port timing (eg GM with perhaps 2 psi of supercharge) but the external pumps you see are primarily for scavenge.Name a 2 stroke that isn't supercharged somewhere in it's system ...
cheapracer, on May 3 2011, 17:22, said:
If you supercharge the hell out of both the 2 stroke will have more power. If you don't supercharge at all, the 2 stroke will have a lot more power. In the small engine category targeted by the PatOP, the latter is a huge advantage as is the balance, efficiency and other benefits mentioned.`You can supercharge the hell out of the PatOP and I can supercharge the hell out of a 4 stroke but only one of them is going to capture the bulk of the volume while the other one is going to blow a considerable amount straight out the exhaust ports - you could add valves to help but then whats the point of the excersize, may just as well build the 4 stroke.
#132
Posted 03 May 2011 - 12:16
A conventional two stroke that controls the intake and exhaust ports by the same piston, has symmetrical port timing.
If the intake ports open at x degrees after the CDC (Combustion Dead Center), they close at x degrees before the CDC. Similarly, if the exhaust ports open at y degrees after the CDC, they close at y degrees before the CDC.
In the opposed piston engines, things are different because different pistons control the intake ports and the exhaust ports.
Take for instance the OPRE prototype engine:
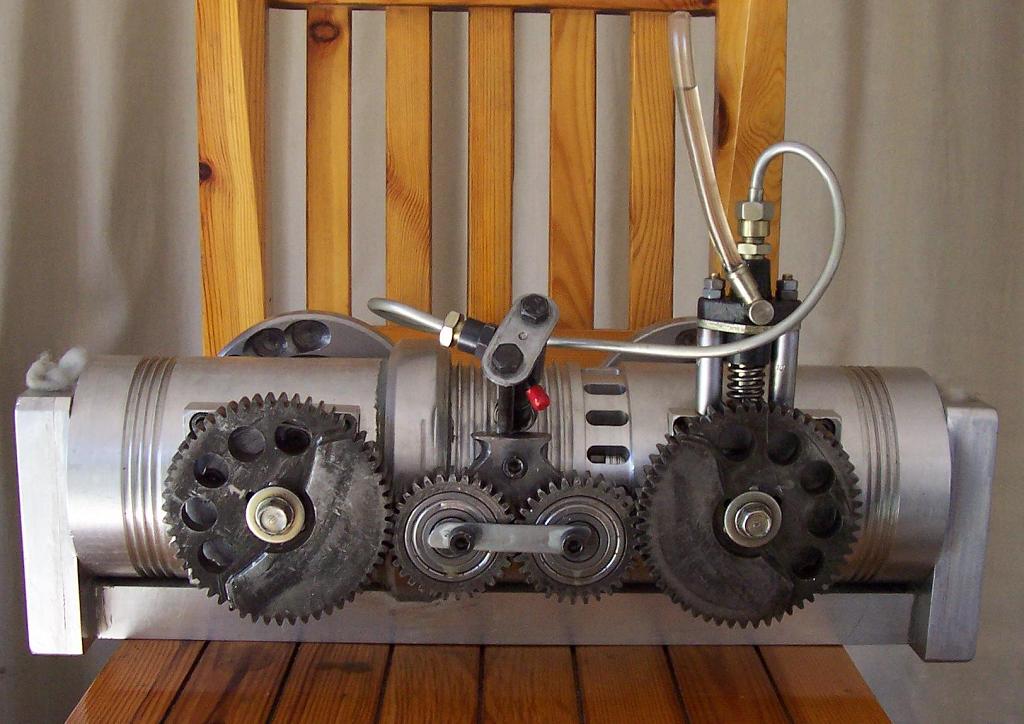
which, in this photo, has symmetrical port timing (the volumetric scavenging pumps fit to this timing).
If you ****** the intake crankshaft, at left, for 2 gear-teeth, which is about 13 crankshaft degrees (all you have to do is, during the assembly of the synchronizing gearing, to “time” differently the gears), you put a significant asymmetry in the port timing (the vibrations increase, but not too much).
The CDC (combustion dead center), i.e. the point wherein the combustion chamber volume is minimized, is at +6.5 degrees of the exhaust crankshaft and at –6.5 degrees of the intake crankshaft (zero degrees for a crankshaft is the angle at which the piston is at the maximum distance from the crankshaft axis).
The exhaust ports open at, say, 100 degrees after the CDC and close at 113 degrees before the CDC, while the intake ports open at, say, 115 degrees after the CDC and close at 102 degrees before the CDC.
In the Junkers Jumo direct injection airplane Diesel engines, the intake crankshaft is ******** for 11 crank degrees. Besides the asymmetrical timing, with such a phase difference most of the power is delivered to the exhaust crankshaft. Those engines are still famous for their excellent scavenging efficiency (pure uniflow scavenging, long stroke, small bore).
In the Deltic opposed piston engine, the geometry made necessary a 20 degrees phase difference between the intake and the exhaust crankshafts. Not the optimum, but it works.
In the OPRE engine, a 7 crankshaft degrees phase difference has the same effect as the 11 degrees in the Junkers Jumo engines, because of the different motion of the pistons. A 7 degrees difference has very small effect on the vibrations, however with a volumetric scavenging pump no phase difference is necessary.
To make the same in the PatOP, the intake crankpins must be angularly displace for 7 crank degrees (alternatively, the crankshaft can be offset relative to the cylinder axis, etc).
You can also take a look at the Commer TS animation, in one of my previous posts. It uses asymmetrical timing, too: the exhaust ports open earlier than the intake ports, the exhaust ports close earlier than the intake ports.
I think the meaning of the asymmetrical timing in the two stroke engines is now clear.
The volumetric pumps and their reed valves are responsible for the “four stroke” breathing of the PatOP and OPRE engines.
In the photo below:

fresh air passes through the “holes net” (at the four corners of the bottom cover) and then from the air filters before it finds the intake reed valves.
The turbochargers have their own limitations that are added to those of the basic engine. A bad characteristic of the supercharged direct injection Diesels is their short rev range: plenty of torque, but in a short rev range. The driver has to deal with the gearshift lever all the time.
Think of a conventional diesel that can make its power band broader by 35%, and how many gearshifts saves for the driver and how much economy it can bring about.
On the other hand, using the same turbocharger in the PatOP engine and in a four stroke of same capacity, the relation of the air passing through the two engines remains the same: 1700 versus 635.
As for the power, the PatOP burns once per crank rotation, has more compact combustion chamber and plenty of time to burn the Diesel fuel at higher revs. For road traffic the wide power band is more important than the peak power.
The four-stroke is a heavy prime-mover chiefly because of the cylinder block, the cylinder head and the studs that must keep them together.
The OPRE, PatOP and OPOC has none of them; their weight is way less than half.
Of course, as two-stroke engines they cannot be quiet, neither clean, nor fuel efficient, and, worse even, nor generally likeable!
Thanks
Manolis Pattakos
#133
Posted 03 May 2011 - 12:58
gruntguru, on May 3 2011, 19:33, said:
.
You are trapped in your experiences of conventional 2 stroke engines. The OP design can scavenge 100% + across a wide rev range.
99% of them. You are confusing scavenging with supercharging. Many have some degree of supercharge courtesy of pipe tuning or some stagger of valve/port timing (eg GM with perhaps 2 psi of supercharge) but the external pumps you see are primarily for scavenge.
If you supercharge the hell out of both the 2 stroke will have more power. If you don't supercharge at all, the 2 stroke will have a lot more power. In the small engine category targeted by the PatOP, the latter is a huge advantage as is the balance, efficiency and other benefits mentioned.`
I think you've finally lost it.
su·per·charge (spr-chärj)
tr.v. su·per·charged, su·per·charg·ing, su·per·charg·es
1. To increase the power of (an engine, for example), as by fitting with a supercharger.
2. To charge heavily or excessively:
vb (tr)
1. (Engineering / Mechanical Engineering) to increase the air intake pressure of (an internal-combustion engine) with a supercharger; boost
2. to charge (the atmosphere, a remark, etc.) with an excess amount of (tension, emotion, etc.)
3. (Physics / General Physics) to apply pressure to (a fluid); pressurize
I don't give a toss what name you use or what plate you serve it on, a 2 stroke WILL NOT RUN without some form of supercharging period. For example the very engines we are discussing - the OPOC utilises an electric turbo to have supercharging from scratch otherwise it wouldn't start as a normal turbo would offer no supercharging at low speeds and Man's engine has internal supercharging via a separate piston otherwise it wouldn't run.
Every common 2 stroke for the last 100+ years from motor mowers to world championship road racers has utilised it's own crankcase for supercharging.
The OP like every other 2 stroke can only have a small effective emission meeting RPM rev range - they have a market for stationary engine use but still can not meet emissions requirements over a broad RPM band thats needed for the common automobile.
Why in every free form of motor/water/airsport are they not using 2 strokes? Why especially in drag racing where they do in fact supercharge the hell out of everything doesn't anybody use a 2 stroke?
gruntguru, on May 3 2011, 19:33, said:
.
Port-timed, single piston 2 strokes have inlet opening centred around BDC, likewise exhaust. The opposed piston design can have two seperate BDC's and therefore an exhaust period centred prior to "average BDC" and an inlet period centred after "average BDC".
manolis, on May 3 2011, 20:16, said:
About the asymmetrical timing in the two stroke engines
A conventional two stroke that controls the intake and exhaust ports by the same piston, has symmetrical port timing.
If the intake ports open at x degrees after the CDC (Combustion Dead Center), they close at x degrees before the CDC. Similarly, if the exhaust ports open at y degrees after the CDC, they close at y degrees before the CDC.
Thanks
Manolis Pattakos
No, any 70's onwards reed valved 2 stroke has variable intake timing sensitive to pressure requirements actually, totally asymetrical and self adjusting. The 80's onwards 2 strokes with the addition of an exhaust valve for height adjustment of course are still symetrical but are able to offer a much wider RPM range of efficiency due to being able to capture the shear point of the gases as the piston closes the exhaust port off over a wider range depending on the finesse of the valve.
Sure the OP can improve things but only slightly, you still can not get away from the simple fact that both ports are wide open for a mighty long time and that only suits a narrow operating range and any great volumes of supercharged air will get blown straight through and out the exhausts - heres a tip I learnt as a kid, when pumping a bicycle tyre up it's best not to have a hole in the inner tube ...;)
manolis, on May 3 2011, 20:16, said:
. PatOP ..... It uses asymmetrical timing, too: the exhaust ports open earlier than the intake ports, the exhaust ports close earlier than the intake ports.
I think the meaning of the asymmetrical timing in the two stroke engines is now clear.
And No again, thats not asymetrical timing, it's simply symetrical timing thats been staggered.
Edited by cheapracer, 03 May 2011 - 14:02.
#134
Posted 03 May 2011 - 13:31
cheapracer, on May 3 2011, 13:58, said:
I think you've finally lost it.
su·per·charge (spr-chärj)
tr.v. su·per·charged, su·per·charg·ing, su·per·charg·es
1. To increase the power of (an engine, for example), as by fitting with a supercharger.
2. To charge heavily or excessively:
vb (tr)
1. (Engineering / Mechanical Engineering) to increase the air intake pressure of (an internal-combustion engine) with a supercharger; boost
2. to charge (the atmosphere, a remark, etc.) with an excess amount of (tension, emotion, etc.)
3. (Physics / General Physics) to apply pressure to (a fluid); pressurize
I don't give a toss what name you use or what plate you serve it on, a 2 stroke WILL NOT RUN without some form of supercharging period. For example the very engines we are discussing - the OPOC utilises an electric turbo to have supercharging from scratch otherwise it wouldn't start as a normal turbo would offer no supercharging at low speeds and Man's engine has internal supercharging via a separate piston otherwise it wouldn't run.
Every common 2 stroke for the last 100+ years from motor mowers to world championship road racers has utilised it's own crankcase for supercharging.
The OP like every other 2 stroke can only have a small effective emission meeting RPM rev range - they have a market for stationary engine use but still can not meet emissions requirements over a broad RPM band thats needed for the common automobile.
Why in every free form of motor/water/airsport are they not using 2 strokes? Why especially in drag racing where they do in fact supercharge the hell out of everything doesn't anybody use a 2 stroke?
No, any 70's onwards reed valved 2 stroke has variable intake timing sensitive to pressure requirements actually, totally asymetrical and self adjusting. The 80's onwards 2 strokes with the addition of an exhaust valve for height adjustment of course are still symetrical but are able to offer a much wider RPM range of efficiency due to being able to capture the shear point of the gases as the piston closes the exhaust port off over a wider range depending on the finesse of the valve.
Sure the OP can improve things but only slightly, you still can not get away from the simple fact that both ports are wide open for a mighty long time and that only suits a narrow operating range and any great volumes of supercharged air will get blown straight through and out the exhausts - heres a tip I learnt as a kid, when pumping a bicycle tyre up it's best not to have a hole in the inner tube ...;)
Like the description cheapy

What if the hole in the bicycle tyre can be opened and closed and sized, when and how big as required?
Edited by 24gerrard, 03 May 2011 - 13:32.
#135
Posted 03 May 2011 - 15:29
manolis, on May 3 2011, 20:16, said:
. PatOP ..... It uses asymmetrical timing, too: the exhaust ports open earlier than the intake ports, the exhaust ports close earlier than the intake ports.
.
gruntguru, on May 3 2011, 19:33, said:
.
Port-timed, single piston 2 strokes have inlet opening centred around BDC, likewise exhaust. The opposed piston design can have two seperate BDC's and therefore an exhaust period centred prior to "average BDC" and an inlet period centred after "average BDC".
manolis, on May 3 2011, 20:16, said:
About the asymmetrical timing in the two stroke engines
A conventional two stroke that controls the intake and exhaust ports by the same piston, has symmetrical port timing.
If the intake ports open at x degrees after the CDC (Combustion Dead Center), they close at x degrees before the CDC. Similarly, if the exhaust ports open at y degrees after the CDC, they close at y degrees before the CDC.
Thanks
Manolis Pattakos
Oh and some of the original 2 strokes using split single arrangement had the same staggered timing 100 years ago ... nothing new under the sun.
http://en.wikipedia....ki/Split-single

These engines makes the OPOC boss a person who speaks untruths as he says quite clearly here "you can only do this in an OP engine" ...
http://www.engineeri...der;search:ford
Edited by cheapracer, 03 May 2011 - 15:40.
#136
Posted 03 May 2011 - 16:14
"there is little difference between the jobs we do, a human body is not so different in method of operation to an engine".
The surgeon replied,
"Try repairing that engine when its running".
I see staggered but 'fixed' port timing.
How about fully variable port timing?
#137
Posted 03 May 2011 - 16:15
John
#138
Posted 03 May 2011 - 16:46
To scavenge with pure air is another thing: it depends on how much this air costs to produce.
The cost depends chiefly on how much air you lose and how much you pay to make it move through the engine.
A turbocharger is not the best way to make it, unless it works at a narrow revs-volume-pressure area (the variable geometries of the rotors and shells make this area broader, but not much; Audi, VW, Daimler etc compromise with or add a supercharger in-line to get round).
OPOC adds an electric turbocharger (as a cure-all remedy) for this illness of the turbochargers.
On the other hand, if something provides you with plenty of air, twice, say, as cheaper as the state-of-the-art turbocharger, this cheap and plenty (at all revs and loads) air can:
Scavenge the exhausted gas, by, say, only 80%, leaving the other 20% of the exhausted gas into the cylinder.
Pass another 60% of fresh air through the cylinder, only to cool the engine from within.
This is the 1.4 (80%+60%) scavenge ratio of the PatOP and OPRE prototypes.
The volumetric pumps, at the other end of the working pistons, are supposed to feed this 1.4 scavenge air at a lower energy-cost than the known turbochargers and than the electrical turbocharger of OPOC.
With this poor 80% fresh air into the cylinder, the diesel 2-stroke can generate (per combustion) more than 80% of the energy of the respective 4-stroke filled with 100% pure air (because of the lower friction, of the increased constant volume portion of the combustion, of the higher volume to surface ratio etc).
It gives a 1,6 times more power-to-volume-ratio for the 2-stroke.
Considering the higher revving of the 2-stroke Diesel with the longer piston dwell at the CDC, it results a more than 2 times higher power-to-capacity-ratio.
The power-to-weight ratio seems well above 3 or 4, which is of maximum importance for some applications, like as a power unit for small airplanes at FlyerPowerUnit
But even for a bike or for a light car such a weight and bulk reduction opens further possibilities for further fuel saving (the weight of the engine is always carried by the vehicle)
On the other hand, the PatFour engine:

without being a two-stroke,
has all of the advantages of the PatOP (like the long piston dwell, the full balance of the inertia forces etc) except the compact combustion chamber.
In fact, it was design to show that the Pinnacle engine needs neither the sleeve valves, nor the second crankshaft.
Because it seems unlike to go for a PatFour prototype, those who are in favor of the four stroke and want to participate in the project, are welcome.
Thanks
Manolis Pattakos
#139
Posted 03 May 2011 - 23:40
Advertisement
#140
Posted 03 May 2011 - 23:43
cheapracer, on May 3 2011, 09:29, said:
So where is the running example of this engine? That is what you always ask for when people suggest unusual engine concepts...Oh and some of the original 2 strokes using split single arrangement had the same staggered timing 100 years ago ... nothing new under the sun.
http://en.wikipedia....ki/Split-single
These engines makes the OPOC boss a person who speaks untruths as he says quite clearly here "you can only do this in an OP engine" ...
http://www.engineeri...der;search:ford
And the key words I see in your last post are "100 years ago". Where are the current models of this engine after 100 years of commercial use? When they say "you can only do this with an OPOC engine, that probably refers to the present day.
I think you should re-examine your bias agains the OPOC motor...
#141
Posted 04 May 2011 - 00:18
unclematt, on May 4 2011, 09:43, said:
There were tens or even hundreds of thousands of the things running around europe a few decades back. That's a twingle. Belligerence has its place but combined with cluelessness it makes for amusing reading.So where is the running example of this engine?
#142
Posted 04 May 2011 - 01:48
#143
Posted 04 May 2011 - 01:52
unclematt, on May 4 2011, 07:43, said:
So where is the running example of this engine? That is what you always ask for when people suggest unusual engine concepts...
And the key words I see in your last post are "100 years ago". Where are the current models of this engine after 100 years of commercial use? When they say "you can only do this with an OPOC engine, that probably refers to the present day.
I think you should re-examine your bias agains the OPOC motor...
I bought and sold 2 of these about 15 years back at a Gatton swap meet http://www.google.co...w...mp;aql=&oq= so I assure you they exist - research NSU 250 from about 1950 through 1970. Actually Google both the 2 and 4 stroke NSUs because both were unusual and even Triumph had a split single.
The great thing about the split single in the present day is I have total control over the combustion chamber shape and spark plug/injector position, 2 things OP engines can't offer as well as the split single also offers 2 pistons in short stroke form but only one crankshaft whereas the OP needs 2. I could also take advantage of reed valve and exhaust port valves as well as exhaust tech not known back then.
You will never see the OPOC engine in a mass production car, it's that simple and it may be seen in military vehicles but thats cause they are playing the right games with the right people not because it's a better thing - theres a lot more to selling to the military than having the right equipment as history has well proven.
The bias I have is against scamming thieves not new tech in itself.
#144
Posted 04 May 2011 - 02:09
Come back to it later, got some race seats to build now ...
NTSOS, on May 4 2011, 00:15, said:
Hey Cheap.......just curious.........do you speak the lingo?
John
Yeah but pretty bad for 6 years here but I get by.
Edited by cheapracer, 04 May 2011 - 02:11.
#145
Posted 04 May 2011 - 02:12
cheapracer, on May 3 2011, 22:58, said:
I repeat - the pump common to all 2-strokes has the function of scavenging not supercharging. If the pressure at BDC is atmospheric or less, the engine is not supercharged. If a GM 2-sroke diesel uses 95% of the blower output to exhaust and refill the cylinder and the remaining 5% to pressurise the cylinder, its function is 95% scavenging and 5% supercharging.I think you've finally lost it.
su·per·charge (spr-chärj)
tr.v. su·per·charged, su·per·charg·ing, su·per·charg·es
1. To increase the power of (an engine, for example), as by fitting with a supercharger.
2. To charge heavily or excessively:
vb (tr)
1. (Engineering / Mechanical Engineering) to increase the air intake pressure of (an internal-combustion engine) with a supercharger; boost
2. to charge (the atmosphere, a remark, etc.) with an excess amount of (tension, emotion, etc.)
3. (Physics / General Physics) to apply pressure to (a fluid); pressurize
I don't give a toss what name you use or what plate you serve it on, a 2 stroke WILL NOT RUN without some form of supercharging period. For example the very engines we are discussing - the OPOC utilises an electric turbo to have supercharging from scratch otherwise it wouldn't start as a normal turbo would offer no supercharging at low speeds and Man's engine has internal supercharging via a separate piston otherwise it wouldn't run.Every common 2 stroke for the last 100+ years from motor mowers to world championship road racers has utilised it's own crankcase for supercharging.
cheapracer, on May 3 2011, 22:58, said:
Don't forget these are diesel engines. They can be made to meet emissions across the full operating range as easily as a 4 stroke.The OP like every other 2 stroke can only have a small effective emission meeting RPM rev range - they have a market for stationary engine use but still can not meet emissions requirements over a broad RPM band thats needed for the common automobile.
cheapracer, on May 3 2011, 22:58, said:
There are many reasons - most often the rules do not allow 2 strokes. Where the rules do allow 2-stroke, the racer still has to find a suitable base engine and have the know-how to modify, prepare and tune it. Where 2 stroke engines are readily available eg boats, karts and (previously) motorcycles, they are used extensively for racing.Why in every free form of motor/water/airsport are they not using 2 strokes? Why especially in drag racing where they do in fact supercharge the hell out of everything doesn't anybody use a 2 stroke?
cheapracer, on May 3 2011, 22:58, said:
No, any 70's onwards reed valved 2 stroke has variable intake timing sensitive to pressure requirements actually, totally asymetrical and self adjusting. The 80's onwards 2 strokes with the addition of an exhaust valve for height adjustment of course are still symetrical but are able to offer a much wider RPM range of efficiency due to being able to capture the shear point of the gases as the piston closes the exhaust port off over a wider range depending on the finesse of the valve.
cheapracer, on May 3 2011, 22:58, said:
That's why its called scavengng - not supercharging. The aim is to achieve 100% fresh charge across all rpm and wide open ports is the way to do that. I repeat - forget your "petrol 2-stroke with pipe" experiences. Try to relate what's happening here to something similar like a Jimmy.Sure the OP can improve things but only slightly, you still can not get away from the simple fact that both ports are wide open for a mighty long time and that only suits a narrow operating range and any great volumes of supercharged air will get blown straight through and out the exhausts - heres a tip I learnt as a kid, when pumping a bicycle tyre up it's best not to have a hole in the inner tube ...;)
cheapracer, on May 3 2011, 22:58, said:
And No again, thats not asymetrical timing, it's simply symetrical timing thats been staggered.

Edited by gruntguru, 04 May 2011 - 02:26.
#146
Posted 04 May 2011 - 02:17
Edited by venator, 04 May 2011 - 02:20.
#147
Posted 04 May 2011 - 02:23
cheapracer, on May 4 2011, 01:29, said:
Tke picture you have posted is clearly a variation of the opposed piton design, having two pistons sharing a common combustion chamber.
These engines makes the OPOC boss a person who speaks untruths as he says quite clearly here "you can only do this in an OP engine" ...
#148
Posted 04 May 2011 - 04:35
Also the Junkers-Doxford (which is the half of the OPOC engine of EcoMotors) was in production for many years, too, as giant marine Diesel engine:
The photos are from http://www.shipsnost...oxford_and_Sons
Cylinder liners of the Junkers-Doxford:

The bottom crankcage:

The crankshaft:

And a complete engine:

Strictly technical, now.
The Twingle is something between the single-piston and the opposed piston engine.
In order to avoid the short-circuit between the intake and exhaust ports of the conventional loop scavenged, it uses two pistons and two cylinder liners side by side.
Then the scavenging process is almost uniflow/through scavenging.
The bad news is that the combustion chamber has necessarily a bad shape.
Worse even, the combustion chamber has – during combustion – far more than double surface as compared to the true opposed piston of same bore and stroke. It is like having a 500cc capacity engine with the thermal losses of a 1000cc. Remember the Indians with the side valves?
Another drawback is the crankcase scavenging (the bad shape and the excessive “dead volume” of the “crankcase scavenging pump” fit to a narrow rev range).
The balance (vibration quality) is also bad.
Another drawback is the increased thrust loads due to the necessary big offset of the two cylinder axes from the crankshaft axis.
Differently thinking: bend the cylinder liner of a conventional opposed piston for 180 degrees to get a Twingle.
Here is the PatOP in comparison:
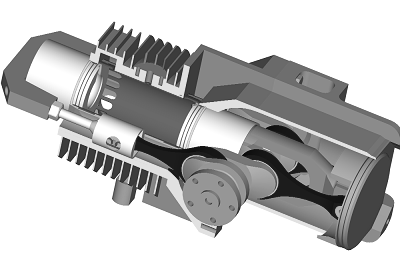
unclematt wrote: “Nice engine manolis, but do you have any concerns regarding squish in this design?”
I think the PatFour has excessive squish.
Take another look at the design, at the flat blue surfaces on the block/liner at right.
As the piston flat crowns get very close to those surfaces – at the end of the compression – most of the charge is violently pushed to the space between the valves.
Thanks
Manolis Pattakos
#149
Posted 04 May 2011 - 05:16
gruntguru, on May 4 2011, 10:23, said:
The picture you have posted is clearly a variation of the opposed piton design, having two pistons sharing a common combustion chamber.
I would think they both came about for entirely different reasons/applications. I'm not here to support the split single merely mentioned that it has staggered timing.
As for scavenging, that is a secondary effect because you have supercharged - positively displaced - pressurised - increased the volume within a given area etc etc, call it what you want but scavenging does not happen by itself in a 2 stroke (well not enough for our purposes anyway such as starting the engine ;) )
#150
Posted 04 May 2011 - 05:24
unclematt, on May 1 2011, 06:35, said:
I read the paper you posted, and I am not seeing anything in it that shows side mounted injectors are problematic. Were there specific passages in the paper you could post to further illustrate your concerns?
unclematt,
The issues with a side mounted injector have to do with the conflicting requirements for nozzle orifice size, injection pressure, spray penetration, spray distribution, fuel mass per injection, time interval for an injection event, droplet size, mixing rate, etc. A modern, conventional DI diesel with a high pressure CR injector typically has a nozzle with up to 8 or 9 very small diameter orifices that are arranged radially, combined with tangential intake charge swirl. This gives a very good fuel spray distribution, with low penetration, very small droplet size, excellent mixing, and minimal ignition delay.
The side mounted injector in an OP engine must have nozzle orifices that are oriented fairly normal to the cylinder axis, so that they do not impinge on the piston crowns at TDC. This limits the number of orifices that the nozzle can have, and in order to get the necessary mass flow per injection the orifices have to be much larger. The larger nozzle orifices produce greater spray penetration and have larger droplet size, which produces sluggish combustion and ignition delay. Also, if there is any intake swirl, there cannot be any sprays directed into that airflow, since the combustion products will be pushed back into the unburnt fuel spray creating lots of smoke.
Of course, there is always the quick fix of employing multiple injectors per cylinder. This is what we did with the TRC OP engine, using two diametrically opposed injectors. The best nozzle geometry we could get in the available tip space was only 3 .012" holes per nozzle. The rail pressure we used was around 20ksi, and we were still getting poor mixing, sluggish combustion, too much penetration, and serious thermal loads on the piston crowns due to impingement.
The paper you read was some CFD work Los Alamos did using the KIVA code. Sandia Labs also made an optical combustion chamber to validate the combustion and injection spray model that Los Alamos did. The prime contractor was Detroit Diesel, and the company I worked for built the single cylinder test rig and did dyno testing. The TRC OP engine was a very high firing pressure (4000 psi) 2-stroke diesel with a 120mm bore. The engine used a low static CR (around 12:1) and very high manifold pressures (>100 psig). As you can imagine, it was a real pain to start. It also ran very rough, was noisy, and shook like heck.
The one problem we never solved was piston ring scuffing. The cylinder liner was a thick wall steel casting to deal with the high pressures. And while it was water cooled, the heat transfer rate through the thick steel wall was never sufficient to prevent the bore surface oil film from flashing off in the area near TDC. The problem was made worse by the limited stroke overlap between the compression ring pack and the oil control rings mounted low on the piston skirts.
Here's a similar OP 2-stroke diesel I designed for General Atomics, back in 1996.
http://www.google.co...E...p;q&f=false
slider